Demand for sanitary napkins is quickly escalating around the world. Sanitary napkin inspection and quality control tests ensure that the product complies with international standards and is safe to use.
Importers typically conduct various on-site product tests during the following stages of manufacturing:
- Pre-production (related: incoming quality control)
- During production
- Pre-shipping / packaging
Key sanitary napkin inspection and quality control tests
Resistance to mechanical penetration test
The resistance to mechanical penetration test measures the force needed to rupture the sanitary napkin. It's also known as the ball burst procedure. Importers of products made with other materials, such as knitted or woven fabrics, will also sometimes conduct this test to measure material strength.
Aerobic biodegradation test
The aerobic biodegradation test determines the degree and rate of biodegradation of sanitary napkin materials in contact with soil, or a mixture of soil and mature compost.
Water retention test
In order to make sure the sanitary napkin satifies the required amount of liquid absorption, the water retention test is performed using the standard ASTM water retention test. This is a basic function test for sanitary napkins that can be done quickly in a factory. It involves immersing the item in water, running it through a centrifuge and comparing the weight before and after.
Flexibility test
Testing the flexibility of the sanitary napkin ensures that the product conforms to international flexibility and manufacturing requirements. The flexibility test follows the standard ASTM circular bend procedure.
These are just a few of the on-site tests commonly performed for sanitary napkins. But the Food and Drug Administration, along with other orgnaizations, recommend various testing that should be performed in a certified lab, such as toxicity.
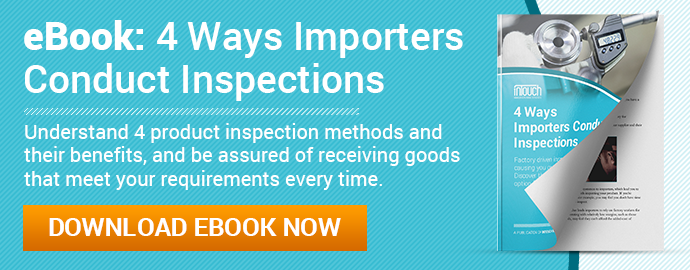