Tires are manufactured on a regular basis due to the fact that the average lifespan of automotive tires, whether it is an automobile, truck, bus, motorcycle etc… can range from 22,000 miles to more than 60,000 miles depending on product quality and driving behavior. Regardless of the type of vehicle, almost all tires are made with the same raw materials and components.
Tire Inspection Process
Every manufacturer follows a specific set of inspection and testing protocols for all of the products to ensure the reliability, durability and overall quality. During the production process, tires in production will be inspected periodically to avoid any unnecessary production anomalies that could take place.
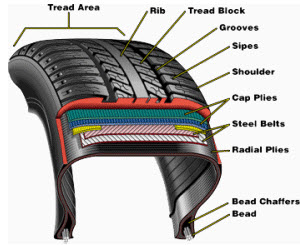
To fully understand the different types of inspection and testing to be conducted during the production process, it is important to know the different types of tires in production. Here are the different types of tires being constructed on a regular basis:
- Bicycle Tires
- Motorcycle Tires
- Automobile Tires
- Construction Truck Tires
- Bus Tires
- Industrial Truck Tires
- Aircraft Tires
Pre-Production Inspection
As per SAE J 332, each machine to be used for composition and manufacturing of different tire types will be thoroughly inspected for any damage or defects and any other potential damaging factors detected. The purpose of this inspection process is to verify that all of the equipment and devices to be used for tire production is in working order to ensure quality products.
Machines that show damage and/or defects should not be used for production to ensure that no production anomalies will take place as much as possible. Machines will either be repaired and/or replaced or will be disposed accordingly.
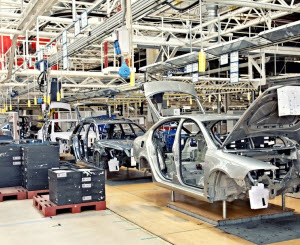
Materials Inspection
All of the materials to be used for tire construction will be thoroughly inspected for any imperfections to avoid defective products the soonest it has been detected. The purpose of this inspection process is to ensure that all of the materials to be used are free from damage and/or defects. The components to be used are:
- Tire Components
- Inner Liner
- Body Ply
- Sidewall
- Beads
- Apex
- Belt Package
- Tread
- Cushion Gum
Materials that show signs of damage or defects will be automatically rejected and will not be used throughout the entire production process.
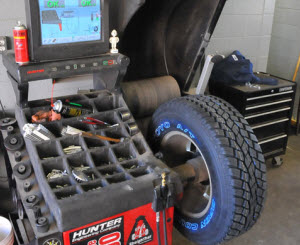
Production Inspection
All of the materials that pass the inspection process will be then transferred to the assembly line where the entire tire manufacturing process is initiated. Throughout the duration of the manufacturing process, each material will undergo different departments before getting the final product. These departments are:
- Mixing and Compounding – rubber materials to be used will be mixed with different agents to form a rubber compound to be used for tires.
- Calender, Extrusion and Bead Building – all of the needed components for tire manufacturing will be prepared during this production queue to ensure all of the materials are complete prior to the next production process.
- Tire Assembly – after all of the materials have been prepared and gathered, tire building will be performed and will be inspected on a regular basis until all of the components are properly coated.
- Curing – all of the tires that are halfway finished will undergo curing process where immense pressure will be applied in a mold in order to create the suitable shape of the tire. By using a machine to assist with the roundness, the success rate of curing items is above 80 percent.
Items that fail to hold all the components together will be automatically considered as “DEFECTIVE” and will not be used for the remaining inspection processes.
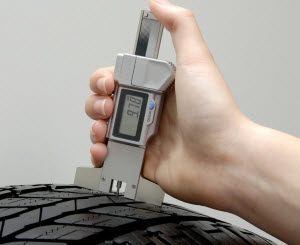
Visual Inspection
After the production process, all of the finished products will undergo a thorough inspection regarding the condition and overall quality and design of each tire. The purpose of this inspection process is to verify that all of the tires out of production show no signs of damage or defects to ensure product reliability and durability as per quality control standards. It is important that each surface area of the tire on queue must be visually inspected and machine tested to ensure that no hidden damage is detected.
- Tread Depth – the surface area of each tire will be inspected thoroughly to ensure that there are no cracks, molds or bubbles detected.
- X-RAY inspection – the internal parts of the tire will be inspected for any underlying defects that could take place during initial use to ensure that all of the tires are structurally sound and reliable right out of production.
Tires that show signs of damage or defects will be evaluated as to the condition of the defective tire. If tire has been proven to be beyond repair, these tires will be considered as “DEFECTIVE” and will not be used for the remainder of the production process.
Weight and Measurement Inspection
All of the tires that have finished the visual inspection process will then be measured and weighed according to its product specifications. Each tire will be measured will deflated and once again once inflated to properly specify the gross and net weight of each tire according to its category.
- Tire Uniformity Analysis – tires under the same category will be measured and weighed according to its product specification to ensure durability, reliability and strict quality control standards.
- Tire balance – tires, regardless of type, will be attached to a machine that emulates the vehicle will be used in order to properly measure the specifications of each tire assembly. Tires that are out of balance will be checked for air pressure and overall build to ensure proper size and weight on all tires.
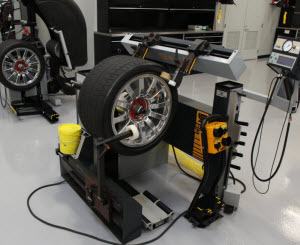
Items that fail the weight and measurement inspection protocol will be evaluated for alternative repairs and reconstruction (depending on the damage) to save overall production time if applicable. Items that are beyond repair will be automatically marked as “DEFECTIVE.”
Final Inspection
The purpose of this inspection process is to verify that all of the tires under the production process will undergo a series of performance and battery tests while maintaining a defect-free product at the end of the testing and inspection phase. The common tests involved for this inspection process are:
- Tire Balance and Performance Analysis – all of the tires will be placed on mechanisms to emulate the vehicle specified to check tire balance and if tires are structurally sound and round.
- Tire rotation analysis – each tire will be put into spinning action to evaluate and analyze the behavior of the tire being inspected while in operation to properly assess the condition of the tire and its overall composition.
- High-Speed Test – all of the tires will be tested on a road-like area where tires will be tested under high speeds to check tire balance and roundness at high speeds of at least 70 miles per hour.
- Damage-Rate Inspection – tires that have finished the entire inspection process will be re-analyzed for any incomplete mold fill and will be checked for damages like blemishes, blisters, exposed cords and other post-production anomalies that have taken place.
Items that fail the final inspection will automatically be marked as “DEFECTIVE” and will be disposed accordingly. Tires that have finished and passed the entire inspection process will be then labeled for its appropriate quality control standard for quality purposes.
[sidebar name="case studies"]