When we talk about the manufacturing process of toilets, it's important to adhere to quality control standards and certificates because they're products that need to perform well daily.
Household toilet types
There are different types of toilets on the market. Some companies choose to differentiate their products by incorporating advanced technology, such as better gravitational pull when flushing. But the general classification method for toilets is by assembly method.
- One-piece toilet assembly – the entire toilet, including the tank, is attached in one coating. One-piece toilets are generally more expensive than two-piece toilet, but they are durable and save on space.
- Two-piece toilet assembly – the toilet bowl and tank are separate pieces that are bolted together. Two-piece toilets are used in most homes because they are cheaper and easier to fix than one-piece toilets.
Regardless of toilet type, most toilets are built, molded and assembled in almost the same way. Following these toilet inspection processes helps you ensure your toilets perform as per quality guidelines.
Materials inspection
This initial part of toilet inspection ensures that all of the needed components for manufacturing the toilet are complete and ready for the next stage of production. Inspection of parts & materials before mass production begins is a process otherwise called incoming quality control.
Assembly inspection
This inspection process checks all of the molded and constructed components made on the assembly line for defects. Minor defects such as cracks, chips and loose parts are acceptable because the factory can generally easily fix them. But toilet systems that have obvious, major or critical defects are labeled as “DEFECTIVE” and disposed of.
Rubber ball test – this test verifies the structural integrity of finished toilets. Regardless of the toilet type, each toilet system is hit with a rubber ball to determine the quality of the toilet. A clear, bell-like ring indicates a good-quality product while a dull ring indicates the toilet was poorly manufactured and is susceptible to leaks.
Visual inspection
Inspecting the toilet's surface area, parts, joints, assembly and structural integrity ensures that the toilet doesn't have any visible damage or defects from the molding and assembly process. Items that are visibly damaged are labeled as “DEFECTIVE” and can be reworked if production time permits.
Toilet bowls are thoroughly inspected for any cracks, deformities, damage and weak bonds to ensure product quality as per ISO 9001 international standards.
Coating inspection
This inspection process checks the pre-coated toilet system for any spots without the proper coating agents prior to the final coating process. Any missed coating spots should be rebuffed on the spot to save production time.
Two-piece toilet systems also require a thorough inspection of their seams to ensure that the entire surface area of the toilet has been evenly coated.
Final inspection
Final inspection is supposed to determine the reliability of the finished toilets. Various tests of structural integrity and functionality are conducted. Each toilet, regardless of type, undergoes the following test:
Maximum performance (MaP) testing – this is a quantitative assessment of the toilet's flushing power, water storage capacity and reliability. The test often uses latex sleeves filled with soybean paste as a substitute to human solid waste. MaP testing consists of the following:
- Each toilet must be able to successfully flush the contents of the bowl. A maximum of 6 trials is conducted to verify the toilet's flushing reliability. Each trial uses a different weight, starting from 100 grams up to 1000 grams of soybean paste.
- Each toilet is analyzed and performance benchmarks should be recorded in order to ensure the product conforms to specifications. An efficiency rating is calculated to ensure MaP testing results are similar.
Quality control standards
Since toilets handle bodily waste on a daily basis, consistent performance is crucial. Toilet manufacturers commonly use these quality control standards when inspecting their products:
ASME A112.19.2 – this standard provides a series of tests pertaining to porcelain plumbing fixtures' materials, dimensions and functionality.
ANSI/ASME 112.3.4-2000 – the standard establishes physical, performance and testing requirements for macerating toilet systems.
Environmental Protection Agency (EPA) WaterSense Standard – the standard is for toilet systems with a manufacturer's claim of water efficiency.
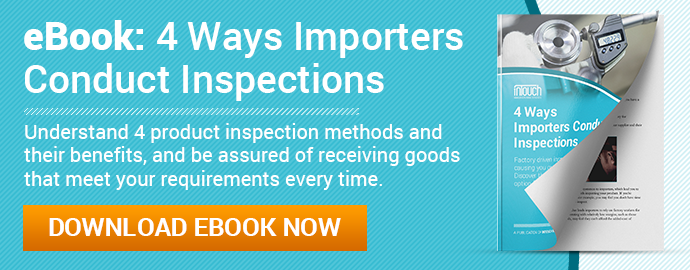