Should you accept or reject this order for shipment? Does it meet your quality standards?
If you’re like most importers, you’ve probably grappled with answering these questions about your product at one time or another. And you likely need a reliable way to assess your product quality, without personally visiting your supplier’s factory and inspecting the product yourself. This is especially true when your order can number in the hundreds and thousands of units. That’s where acceptable quality levels (AQL) can be useful for inspection.
Using AQL, you can check whether an order meets your quality requirements without having to inspect every unit of the entire shipment, saving you time and money on inspection. But one look at the AQL table could leave you feeling lost among the mass of numbers, letters, labels and even colors. Is this a quality control tool or a brain teaser?!
Many explanations of AQL use advanced math models and equations to show how to choose a statistically significant sample for inspection. And these explanations can be hard to follow and overly complex if you’re just looking for a practical introduction on how to use AQL.
But fret not. By the end of this article, you’ll be equipped with all the information you need to get started with using AQL for inspection. And if you’re looking for a more comprehensive look at how AQL affects your inspection results, check out our eBook, The Importer’s Guide to Managing Product Quality with AQL.
1. Acceptance sampling
Acceptance sampling is a way to pull and check a random sample of goods or material and accept or reject the total lot based on a statistical result. This lets you apply the results of inspecting this representative sample to making a decision about whether to allow your supplier to ship an order. AQL sampling is one type of acceptance sampling widely used in product inspection (related: Why QC Professionals Use AQL Sampling for Product Inspection).
For example, rather than inspecting 100 percent of an order of 1,200 pairs of jeans to decide if the order meets your quality expectations, you could make a similar decision by randomly checking only 80 pairs using acceptance sampling.
Why use acceptance sampling instead of inspecting 100 percent or a fixed percentage?
While 100-percent inspection might sound appealing because it provides the largest scope of oversight, it’s often better to use acceptance sampling when:
- Product testing is destructive – it’s better to test a sample of the total lot when testing destroys the product. In fact, acceptance sampling first emerged as a popular QC method when the U.S. military needed a reliable way to test samples of bullets during World War II.
- 100 percent inspection is costly or tedious – especially when hiring an independent inspector, more time spent checking your products often raises your costs.
Acceptance sampling requires certain sample sizes and standards. And if you instead inspect a fixed percentage of your order, say 10 or 20 percent, you might check more units than needed to get the same results. Due to the statistics behind acceptance sampling, you can actually check relatively fewer units as your lot size grows and still have similar confidence in the results.
2. Acceptable quality level (AQL)
Acceptable quality level (AQL), also referred to as acceptable quality limit, is the minimum quality level a shipment is required to meet for an importer to accept it. It’s one of the most commonly used tools among quality control inspectors to measure an order’s conformance to your requirements. Acceptable quality levels typically range from 0 to 15, though AQLs higher than 6.5 are rarely used in the field. The higher your acceptable quality level, the higher your tolerance for quality defects in your order.
Quality control professionals and importers commonly use the AQL table to calculate important factors for inspection. This table tells you the appropriate number of units to pull for inspection, or your sample size, and the number of defects that would be acceptable in that sample. You can also use an online AQL calculator to find these based on your own order quantity and quality expectations.
You’ll almost always find some defects in your sample when inspecting consumer products—few, if any, factories have perfect and consistent production processes. But because not all quality issues are equally serious, you’ll probably assign different AQLs to different types of quality defects (see critical, major and minor defects below).
What if your product quality doesn’t meet your AQL?
If the product quality of your order is found to be worse than your chosen AQL, resulting in a failed inspection, you might ask the supplier to hold the shipment. Here importers will typically address quality issues in one of several ways, such as:
- Asking their supplier to rework or repair the affected units to meet their AQL, if such rework is practical and unlikely to lead to further defects,
- Asking their supplier to replace the affected units,
- Charging back their supplier for unsellable goods, or
- Destroying any unsellable units to prevent their supplier from selling them on the black market or to their competitors
The way you choose to address a failed inspection will largely depend on the strength of your relationship with your supplier, the severity of defects found, the value of your order and the urgency to ship.
3. ANSI-ASQ Z1.4
ANSI ASQ Z1.4 was developed by the American National Standards Institute and American Society for Quality, and it’s the most widely used standard for AQL sampling (related: Alternatives to ANSI ASQ Z1.4 for AQL Sampling During QC Inspection). The U.S. FDA recognizes this standard as applicable for single, double and multiple sampling plans. But most importers use it for single sampling plans. This means inspectors only pull one sample at random and issue a result based on the quality of this sample.
ANSI ASQ Z1.4 is based on inspection by attributes. This means inspected units are evaluated under two categories, either “conforming” or “nonconforming” to your requirements. Variable sampling instead measures the degree of nonconformance, based on sample standard deviation or sample range measurements. ANSI ASQ Z1.9 is the most commonly used standard for inspection by variables.
4. General inspection level
Now let’s dive into the process of how to use the AQL table for inspection. Inspection levels determine the sample size, or number of units the inspector will check on site at the factory. The bulk of your inspection will involve checks on the sample size associated with a general inspection level, like checks for appearance, assembly and functionality. In order to use the AQL table to determine your sample size, you’ll need to know your lot size, or total order quantity, typically shown on your PO. Sample sizes can range from 2 to 2,000 units, depending on your lot size.
General inspection levels are divided into three levels based on inspection scope:
- GI – the smallest sample size available for your lot size, this is the “budget option” offering the least transparency in the least amount of time
- GII – the “middle-ground” option that balances time and cost with transparency, this is the most common inspection level for importers
- GIII – the largest sample size available for your lot size, this offers the most transparency into your order’s quality and takes the most time to inspect
You might approach inspecting your product for the first time using the common “GII” inspection level. But whichever level you choose, you can always adjust it for later inspections based on earlier results. For example, if your supplier consistently meets your quality standards and orders are easily passing inspection, you might lower the inspection level. Whereas if your goods are repeatedly failing or narrowly passing inspection, you might raise the inspection level.
5. Special inspection level
Special inspection levels are reserved for tests that you only intend to conduct on a comparatively smaller sample size than the general inspection level sample size. Whereas you’d use a general inspection level for tests and checks that are relatively quick and easy to perform, you’d use a special inspection level for tests that:
- Are destructive to the product, like a fabric GSM test that involves cutting out a piece of fabric from the sample
- Are expensive and/or time consuming to conduct, like a battery charging test for electronic devices
- Tend to yield similar results across all units, like measuring the dimensions of injection-molded components that don’t vary appreciably in size from one unit to the next
Unlike the three general inspection levels, there are four special inspection levels, based on your desired inspection scope. Similar to general inspection levels, S1 is the smallest sample size for your lot size and S4 indicates the largest sample size. You might inspect a larger or smaller sample size depending on how important a test is for evaluating your product.
6. Critical defect
Critical defects are the most serious of the three main classes of defects QC professionals use for product inspection (related: 3 Types of Quality Defects in Different Products). When applying a unique AQL to each defect class, importers typically use an AQL of 0.0 for critical defects, representing zero tolerance. This means that the entire order will fail inspection if inspectors find a single critical defect in the sample.
QC professionals typically define defects as “critical” if they:
- Pose a safety hazard to the end customer
- Render the product unusable, and thus unsellable
- Often cause product recalls
Samsung’s now infamous exploding batteries in their Galaxy Note 7 would have been a critical defect, if found during inspection. Other examples of critical defects can include:
- Mold on packaging or product
- Incorrect barcodes
- Needles left in a garment
- Rust found on industrial products
- Exposed nails or sharp edges
Because of the risk and severity of problems critical defects pose, most importers will insist on replacing or reworking any goods found with critical defects and then re-inspecting before shipment.
7. Major defect
Less serious than critical defects, major defects tend to be acceptable in limited quantities but are still a concern. The most common AQL importers assign to major defects is 2.5, though you may choose a different AQL based on your own tolerance for defects. Inspectors typically consider a product defect to be “major” when it:
- Adversely affects the performance of a product
- Varies significantly from product specifications
- Would likely cause the end customer to return the product
Major defects aren’t likely to endanger consumers or lead to product recalls. But they can still hurt customer satisfaction, and ultimately, sales. Examples of major defects include:
- Holes or tears in a garment
- Obvious damage to a polybag
- Dimensions out of tolerance for industrial components
- Wobbling or uneven legs in an item of furniture
- A crack in a LED screen
- Dirt, discoloration or excess glue on a product that can’t easily be removed
Goods can fail inspection due to a quantity of major defects found beyond your tolerance (see rejection and acceptance point below). When this happens it’s common for the supplier to eliminate enough major defects—typically through product replacement, repair or rework—such that the quantity found upon re-inspection is within the tolerance set by the AQL for major defects.
8. Minor defect
Major defects are the least serious of the three defect classes. But your goods can still fail inspection if the number of minor defects found exceeds your tolerance set by AQL. An AQL of 4.0 is typical for minor defects, though you may choose a stricter or looser AQL. Typically, minor defects are relatively small or insignificant issues that:
- Do not affect the product’s functionality or form
- Are not noticeable to the customer upon unpacking the product
- Would be unlikely to cause a customer to return the product based on the presence of one minor defect alone
Despite their lower severity, a large quantity of minor defects in your product can still have a negative impact on sales and how your customers view your brand, especially if you’re selling your product at a high price point. Examples of minor defects include:
- Untrimmed threads on a garment, furniture upholstery or plush toy
- Minor color deviation within packaging
- Illegible graphics on retail packaging
- Removable dirt, dust or excess glue on an item
- Poor coating of polish or veneer
Some quality issues can be classified as either a minor or a major defect, depending on the severity of the issue or the prevalence in the sample. For instance, you might consider a scratch in a ceramic dish to be a minor defect if less than 2cm long and major if 2cm or longer. Likewise, you might consider the same issue to be a minor defect that another importer manufacturing a similar product considers to be a major defect.
9. Acceptance point
Typically denoted as “Ac” in the AQL table, the acceptance point indicates the maximum number of defects allowed in a given sample size and at a given AQL to accept an order. Just as many importers assign a different AQL to each of the three defect classes, they’ll also have a different acceptance point for each. Most importers have a higher acceptance point for minor and major defects than for critical defects, reflecting the range in AQL values they choose.
A sample conforms to your selected AQL if the number of defects found is equal to, or less than, your acceptance point for that defect class.
10. Rejection point
Typically denoted as “Re” in the AQL table, the rejection point indicates the minimum number of defects in a given sample size and at a given AQL to reject an order. The acceptance point and rejection point go hand-in-hand. And your rejection point will always be one value higher than your acceptance point when using a single-sampling plan.
If the number of defects found is equal to, or greater than, the rejection point, the sample does not conform to your chosen AQL for that defect type. Typically, importers will respond by rejecting, or asking their supplier to hold, the order until enough defects are remedied to pass re-inspection.
Conclusion
As with using any sampling plan, your transparency and the accuracy of results are limited by the size of the sample taken. And there’s always a risk that you might reject “good” lots or accept “bad” lots when making shipping decisions based on the results of acceptance sampling (related: What QC Inspection Results Do and Don't Mean for Your Shipment).
But using an inspection method based on acceptance sampling, like AQL, ensures that you don’t inspect more goods than necessary, and in turn, don’t spend more time or money on inspection than needed. And for most importers, the relatively low risk inherent in checking a sample heavily outweighs alternative ways of inspecting their goods before shipment.
Send us your questions about using AQL for inspection in the comment section below!
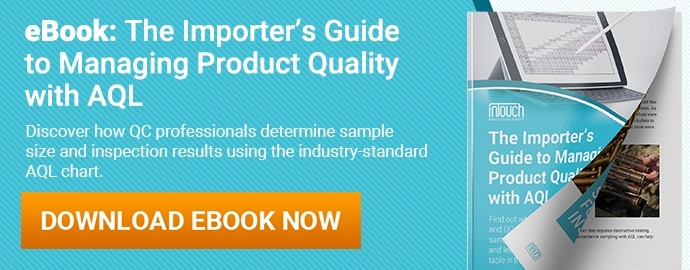