Best in Manufacturing – January 14, 2018
Each Sunday, we publish a list of top articles and other content related to manufacturing in areas like quality control, product development, supply chain management, sourcing, auditing and law.
1. CNY 2018: ready for supply chain havoc?
The time is nearly upon us: Chinese New Year (CNY). This year, the holiday runs from February 15-21, but many supply chains are affected for longer than just that.
To those in the manufacturing industry or familiar with global trade, this holiday is a major disruption. The mega-factory that is China comes to a grinding halt. Similar disruptions also occur around this time in Korea, Vietnam, Laos, Singapore and many other Asian that celebrate Lunar New Year.
This major slowdown isn’t the end of the world…so long as you prepare for it. Ensuring your business can continue undisturbed by any disruption to your supply chain requires planning and not underestimating the holiday.
The author of this featured article has a few reminders to help you weather the storm:
- Book your cargo shipment date well in advance (right now if you haven’t already!) so you can avoid the premiums logistics companies charge
- Your main factory may use subcontracted factories to help meet demand before CNY. Consider one of the ways that importers conduct product inspection to verify your order is at the quality you want and production is on track there
- Keep a close watch in February, March and April for any drop in quality that often occurs after factories hire new, less skilled workers
- And more!
Don’t get burned by CNY. Read the featured article in the link below for some ideas for how to keep your supply chain healthy and running around CNY:
Supply Chain Managers Should Now Prepare for Chinese New Year – Rosemary Coates, Supply Chain Management Review
2. Eliminating PCBs with MIDs
If you pry open any modern electronic device, there’s a high probability you’ll find a printed circuit board (PCB) inside. Devices need PCBs to connect electronic components and allow energy to transfer. Without PCBs, many products would be nothing more than a plastic shell, devoid of functionality.
In contrast to PCBs, there are molded interconnect devices (MIDs). These devices possess the mechanical structure required for an item in addition to the substrate required for conductive traces between electrical components. And most importantly, they don’t possess any wires.
MIDs, according to the featured article, have been around for several years. But what makes them more appealing now is their decreasing cost to manufacture. As more engineers and designers begin to favor MIDs, suppliers will have an incentive to use and adapt MIDs to better serve their customers.
The featured article mentions two methods of making MIDs:
- Laser direct structuring: a part is made with an injection mold. A laser beam then hits the part, which creates tracks that are eventually given a chemical bath. After the bath, you’re left with conductive tracks.
- Screen printing: you can watch the video below to get an idea of how this process works. When it comes to MIDs, traces and electronics are placed in a way similar to screen printing (be sure to check out the featured article for photos).
You need complete information to determine if MIDs are right for your products. And to get that knowledge, you can check out the full article in the link below:
Will Your Next Circuit Board Come out of a Mold? – Lee Teschler, Design World
3. Precious metal recovery for sustainable manufacturing
There are trace amounts of precious metals, like tungsten, tin, tantalum, gold and others within many electronics. Unfortunately, many of these materials are lost when they’re discarded. And while there’s probably not enough gold in your devices to make you a millionaire, in the aggregate, the devices have enough materials to be re-used in manufacturing.
For reference, the United States Environmental Protection Agency (EPA) reported that by recycling one million cell phones alone, more than 20,000 lbs of copper, 20 lbs of palladium, 550 lbs of silver, and 50 lbs of gold could be recovered. That’s a significant amount of natural resources that consumers would otherwise waste.
This featured article looks at how Dell is making use of those discarded metals by integrating them into its supply chain. Specifically, the company wants to make 6 million new motherboards. Dell is also making a small line of gold jewelry to raise awareness about electronic waste (“e-waste”) and its recyclability.
Dell is taking a proactive approach toward combatting e-waste. But one company can only do so much. To conserve precious metals more effectively, more consumers need to recycle their electronics. Manufacturers and importers can help in this effort by promoting “cradle to cradle” product designs, along with advising end users to recycle their used goods.
If you’re curious about more sustainable manufacturing, check out the article in the link below:
These Rings Are Made From Gold Salvaged From E-Waste – Adele Peters, Fast Company
4. Boosting the speed of 3D printing
Additive manufacturing (also referred to as 3D printing) is pretty nifty. You can create a wide range of objects that would otherwise be impossible to make due to their complex features and geometry. Although 3D printing opens up a whole new world of design possibilities, there are a few common complaints about it, such as the excessively slow process needed to make an item.
Sure – additive manufacturing allows the creation of amazing new products and prototypes. But 3D printing doesn’t yet possess the speed many manufacturers want for mass production. For businesses to adopt 3D printing en masse for their operations, a speed upgrade is necessary.
And thanks to the work of researchers at Lawrence Livermore National Laboratory, that boost might be a step closer to reality.
The researchers have developed what they call “volumetric printing”. Essentially, three separate laser beams flash into a photosensitive resin. The beams harden the resin in about 10 seconds, and after removing excess resin, a complete part remains.
This method benefits from “low cost, flexibility, speed and geometric versatility”. Additionally, volumetric printing reduces the need for part post-processing and supports to prop up a part.
Interested in this new 3D printing method? Check out the full article in the link below to find out more:
Volumetric 3D Printing Injects Speed into Additive Manufacturing – Stephen Mraz, Machine Design
5. The future of ASEAN manufacturing
The Fourth Industrial Revolution (4IR) holds great promise for manufacturing. Over the coming years, it could affect a great swath of the products we consume. Entire economies will be subject to the massive disruption of 4IR.
While the 4IR will bring leaps in productivity and efficiency, such improvements will also affect how developing economies grow. In the past, countries like Japan, China and South Korea (to name a few) used manufacturing to develop and mature. Cheap labor, like in the case of China, served as a beacon for importers to manufacture there.
Several ASEAN member states have the benefit of cheap labor costs. But unlike in the past, they must compete with the competitive force that is the 4IR. Instead of moving manufacturing operations abroad, 4IR’s benefits could in some cases keep businesses where they are or move them to where technology is the most advanced and aligned with their needs.
Vietnam, Cambodia and Indonesia are the ASEAN members that have the highest numbers of workers at risk from automation. These countries, and the other ASEAN members, need to overcome these challenges pointed out by the featured article:
- Being perceived as less responsive to technical change
- Relying on low labor costs as a source of competitive advantage
- Attracting new business in the face of greater productivity and reduced costs elsewhere
Surmounting these challenges is critical for the future of ASEAN’s manufacturing. ASEAN members need to adopt 4IR technology quicker or risk losing their place in the global economy.
To learn more about the future of manufacturing in the ASEAN member states, check out the article in the link below:
ASEAN in the Next 50 Years: How the Region Can Remake Its Future in Manufacturing – Shirley Santoso, World Economic Forum
We’re constantly scanning the web for top manufacturing stories and news. If you’d like to submit an article for consideration for our weekly Best in Manufacturing, send us a message and let us know.
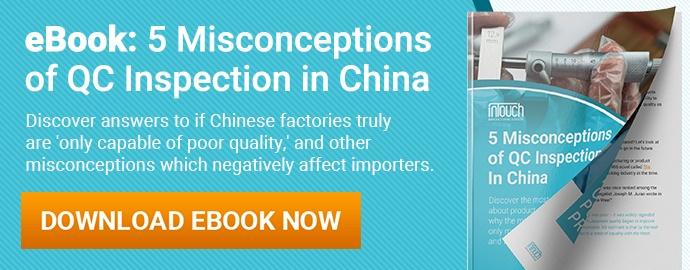