What portion of units with defects would you consider acceptable in a shipment of goods you’re importing?
If you’re like many importers, you might strive to manufacture products with as few quality defects as possible. If you’re very new to importing, you might even expect your goods to be completely free of defects. But the reality is that factories everywhere in the world almost always manufacture products with some defects and nonconformities. An understanding of AQL sampling will help you get the best quality possible (related: The Importer’s Guide to Managing Product Quality with AQL [eBook]).
AQL stands for acceptable quality level, or acceptable quality limit. In basic terms, AQL represents the minimum quality you’re willing to tolerate in an order. Your first instinct might be to choose the lowest AQL, in hopes of assuring the factory produces goods of the highest possible quality. But when you send an inspector to check a shipment at the factory, your chosen AQL will most likely be reflected in the report they issue to you.
By setting an unreasonably high standard for quality that your supplier can’t meet, the order will likely fail inspection. Let’s look at how AQL and other factors to determine the result of your inspections and how you can use that result to make a decision about shipping or holding an order.
AQL sampling results vs. overall inspection results
Most product inspection reports that use AQL will highlight two results—an AQL result and an overall result. While an AQL result of “pass” is a necessary condition for an overall result of “pass”, it’s not the only condition. There are also other factors that determine the overall result of a product inspection. And knowing the difference between these will help you to understand your inspection report and the role AQL plays in the result.
Understanding the role of AQL sampling in determining pass or fail
AQL is a type of acceptance sampling, a quality control process dating back to World War II. The U.S. military used sampling as a method to efficiently test a fraction of a product shipment. Then, based on those results, they were able to make conclusions about the average quality of the total order. This same process has allowed the military—and countless importers since—to reliably control quality without needing to inspect every unit of an order. Let’s look at how AQL sampling helps determine inspection results.
Setting your tolerance for quality issues with AQL
QC professionals use AQL to represent the customer’s tolerance for defects. For example, importers buying low-cost promotional goods tend to have a relatively high tolerance for quality defects. They might use an AQL of 4 or 6 for certain types of defects. Conversely, importers buying more expensive products or working in quality-strict industries, like aerospace, often use a lower AQL between 0 and 1 for certain defects.
Importers will have specific limits to the number of defects allowed in an order, depending on their chosen AQL. These are dictated by accept and reject points corresponding to a given AQL and sample size shown in the AQL table. For example, if your sample size is 80 units and your AQL is 1, your accept point is 2 defects and your reject point is 3 defects. This means that if inspection finds 3 or more defects in a random sample of 80 units, the AQL result will be fail (related: How Importers Use the AQL Table for Product Inspection).
Using different AQLs for different classes of defects
QC professionals generally separate different defects based on severity, applying a different AQL to each defect type (related: 3 Types of Quality Defects in Different Products). Inspectors often pull a single sample to check for all defect types, but each defect type will often have its own accept and reject point. Here are the three classes in which inspectors commonly separate and report defects:
- Critical – defects which violate regulations or can cause serious harm to the user or their property. For example, inspectors typically report a sharp edge on a product as a critical defect given the hazard it poses to consumers.
- Major – defects that will likely result in product returns from customers but do not represent a safety risk to the user. For example, inspectors might report failure of a basic function of a product, like volume control on a mobile phone, as a major defect.
- Minor – defects that don’t affect the product’s function and aren’t likely to result in product returns. For example, a small scratch mark found in the enamel of a skillet might count as a minor defect to some cookware importers.
Importers commonly choose a lower AQL for critical defects and a higher AQL for minor defects, with a third AQL somewhere in between for major defects. Sometimes inspection reveals more defects of a particular class than the acceptable number of defects (accept point) determined by the AQL for that class. In such cases, the AQL result is “fail” and you can conclude that similar defects affect an unacceptably high percentage of the entire order.
Other factors that commonly affect the overall inspection result
The overall result is typically the first one you’ll see when viewing an inspection report, and it’s the one importers are mainly concerned with. The AQL result largely determines the overall result, but there are other factors at work as well. An inspection report can show an overall result of fail, despite having an AQL result of pass. Let’s explore what issues outside AQL sampling might contribute to this result.
On-site product testing conducted on a small sample
Most products are subject to a number of industry-specific, on-site tests during inspection. Some tests are relatively easy and efficient to perform, like testing the zipper on a garment or turning an electronic product on and off once. Inspectors often perform these tests on what’s called the “general inspection level” sample size, or the main sample size for inspection. These test results tend to appear as part of the AQL result.
Often there are other tests which, though necessary, are also time consuming, costly or destructive to the product itself. Inspectors typically perform these tests on a much smaller sample size, sometimes determined by a chosen “special inspection level”. For example, fabric composition testing for garments is usually only necessary for 3 units or fewer because composition typically doesn’t vary significantly across units in the same batch, and composition testing is often destructive.
The results of these tests aren’t reflected in the AQL result and are reported separately. An order can pass for AQL, but fail overall for not meeting the requirements of an on-site product test. This often happens when testing a product against certain claims made by the manufacturer, such as testing watches for water resistance up to a certain depth. In this example, product tests are essential to determining whether the product is sellable. And that’s why the overall inspection result considers testing results.
General packaging requirements
Inspectors often include packaging requirements which are specific to a particular SKU in the AQL result. For example, different product lines in the same order may be distributed through different retailers, which often have their own packaging requirements. Failure to meet these requirements may be shown in the inspection report as defects in the AQL section.
Other packaging requirements are more general. Failure to meet any of these could result an in overall inspection result of fail, regardless of the AQL result. For example, you may have a strict requirement that factory workers label shipper cartons with printed stickers, rather than hand written markings. Any issue here would likely affect all or most of the shipment and would likely affect the overall result of inspection.
Nonconformities omitted from the QC checklist or other specifications
An inspector might find nonconformities or other issues that you didn’t include in specifications or your QC checklist. Inspectors may find that a product’s color doesn’t closely match the color of an approved sample you provided for comparison, for example. If these inconsistencies aren’t categorized as defects that fall under the classes used for AQL, inspectors will often cite them separately in the report.
If there are previously unspecified nonconformities in the order, you’ll often receive a “pending” result, rather than a clear pass or fail result. This is usually because, without having clear guidance on how to report these particular issues, inspectors don’t know how serious you consider them to be. They often need your feedback to clarify these before they can report a pass or fail result in the future.
Deciding whether to accept an order based on inspection results
Contrary to a common misconception, inspection results don’t dictate shipping decisions. They merely empower importers to make informed decisions. As the importer, you’re ultimately responsible for deciding whether an order is acceptable to ship (related: What QC Inspection Results Do and Don’t Mean for Your Shipment).
The best way to ensure that your inspection results reflect your quality standards is to provide all relevant specifications and inspection criteria to QC staff prior to inspection. For inspections based on AQL, you’ll also want to decide which AQL to use and advise your inspection team accordingly. In general, three major considerations govern the shipping decisions of most importers:
Meeting customer expectations for your products
You should aim to set inspection criteria and AQLs that reflect your customers’ expectations of your product. You’re probably quite familiar with what your customers expect from your product, and these expectations tend to depend largely on your price level and product type. An importer selling high-end jewelry, for example, is likely to have a relatively strict AQL. Whereas an importer selling lower-cost, plastic dinnerware is more likely to be lenient with the quality of the goods that ship.
It’s not uncommon for importers to make a shipping decision contrary to inspection results, if those results don’t accurately reflect their customers’ expectations. In fact, you’ll probably need to adjust your AQL standards to be more or less strict as you continue production, particularly if you’re manufacturing a new product. Inspection results tend to adhere more closely to expectations as you inspect the same products repeatedly.
Meeting regulatory requirements in your market
Sometimes the need to meet regulations can override a passing inspection. For example, the U.S. Food and Drug Administration regulates the quality of medical devices, due to safety concerns. They consider an AQL of 1.5 to be the minimum level of quality acceptable for surgical gloves. They accept a more lenient AQL of 2.5 for patient examination gloves, since these are worn in a lower-risk environment.
Other examples of heavily-regulated products are fire alarms, sprinklers and carbon monoxide detectors because of the potentially severe consequences of the product malfunctioning. If inspection criteria don’t include conformance to regulations, you might reject an order, even if the overall inspection result is pass. Keep your QC team updated on any regulations your product must meet, to ensure that inspection results accurately reflect these.
Considering the time and cost needed for any corrective actions
The third main consideration for accepting an order is the time and cost needed to perform any corrective actions for a shipment. If you’re importing injection-molded, plastic displays from a factory in China, for example, the product might fail inspection due to a high number of flow marks found, a minor defect. Like many importers, you might consider whether factory workers can repair or rework the affected units.
But this particular defect is basically impossible to mend. The factory would need to produce entirely new units to replace those with the visible flow marks. This may not be reasonable given the additional time and cost involved, especially if you urgently need to ship the order. Despite the failed inspection, you might ask your supplier to ship the order anyway, deciding that the benefits of shipping the goods as they are outweigh the costs of corrective action.
Inspection reports are meant to be a guide for helping importers determine if an order is acceptable for shipment. They aren’t indisputable authorization from your inspector or third-party QC company to your supplier to ship an order. Reports often prominently display an overall result, such as pass, fail or pending. But you should still practice due diligence in reading through the details of the report, especially when the result is pending.
Conclusion
By using AQL sampling for product inspection, importers can set clear allowances for potential defects found in an order. AQL results are a major determinant of the overall result shown in a typical inspection report. But they’re not the only factor. Understanding how AQL and these other factors affect the results of an inspection enables you to decide how to act on the information inspection provides. And when you’re well informed about AQL and its implications, it’s much easier to manage the quality of your products and give your customers what they want.
Do you have any questions on how AQL results might affect your decision to ship your order? Let us know in the comments below!
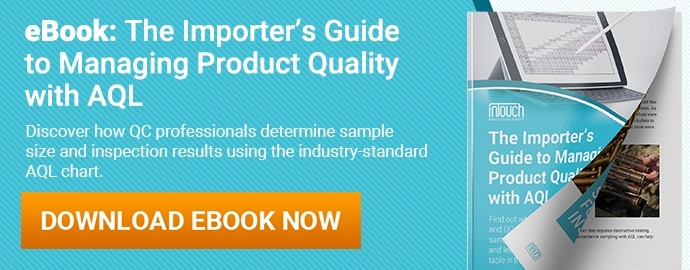