How important is cost when evaluating third-party inspection options?
For most importers, cost is a major factor. You probably don’t want to take the chance of shipping your goods to customers without verifying the quality first. At the same time, you don’t want to pay more than necessary to get a reasonable inspection scope.
Managing costs can be challenging for importers working with one of dozens of professional QC providers offering their services. The best QC provider for you may be one that’s conscious of your budget and willing and able to work with you to accommodate it.
Let’s look at some of the ways Asia Quality Focus (AQF) can help you balance your QC inspection needs with your budget. But first, a short explanation on what determines how much you pay for third-party inspection.
How are third-party inspection services billed?
Most third-party QC providers, including AQF, will bill you for their inspection services using what are called “man-days”. Man-days are a unit of time for measuring how long one inspector is needed for a service. The number of hours in a man-day can vary by QC provider.
But an inspector doesn’t spend all their time billed checking your goods. There are also several other necessary steps in the inspection process that are counted in that man-day, including:
- Traveling to the factory or inspection site (often for an hour or more)
- Preparing the inspection area, which can vary depending on the readiness of the facility
- Pulling a random sample of goods (when using acceptance sampling)
- Writing the inspection report on-site
- Submitting the report to technical staff in the home office for review and approval
- Returning from the factory or inspection site
All of these activities take time and all contribute to the time allotted in a standard man-day. And depending on the time needed for these, your inspector may have less time to actually examine and test your product than you might expect.
How the number of units inspected affects your inspection costs
The quantity of units to inspect is a major determinant in how much you’ll pay for inspection. The larger the sample size, the more man-days required for inspection.
For most consumer goods, it’s usually impractical to inspect 100 percent of an order of hundreds or thousands of units. Instead, third-party QC providers will often suggest inspecting a random sample from which the overall quality level of the shipment can be inferred. AQF and many other QC providers commonly use acceptable quality levels (AQL), a system based on acceptance sampling, to determine a statistically significant sample size (related: The Importer’s Guide to Managing Product Quality with AQL [eBook]).
But within the AQL system, there are also different levels of sampling: three general inspection levels (GI, GII and GIII) and four special inspection levels (S1, S2, S3 and S4). These inspection levels determine your sample size, and in turn, the man-days needed for inspection.
AQF optimizes your AQL sample for inspection scope and cost
If you’re like most importers concerned about their product quality, you probably want the highest level of oversight possible at the lowest cost. You want to limit your risk of unknowingly shipping defective or substandard products to your customers. But you don’t want to spend so much on quality control that you have little or no margin leftover.
AQF helps you balance your inspection scope with your budget by giving you options.
Let’s say you’re manufacturing 5,000 pairs of hiking boots at a factory in Dongguan, China. Based on this lot size of 5,000 pairs, AQF might offer you the following inspection options based on the AQL chart:
- Inspect a GI sample size of 80 pairs in 1 man-day
- Inspect a GII sample size of 200 pairs in 1.5 man-days
- Inspect a GIII sample size of 315 pairs in 2 man-days

Adjusting testing procedures and sampling to meet your goals
On-site product testing can also have a considerable impact on the time needed for inspection. Some products might only require simple tests the inspector can perform in under 10 seconds, like the wet/dry crocking test for fabrics. But some products require more complicated, tedious tests, such as diagnostics testing for mobile phones and tablets.
AQF adapts the testing procedure and sample size to your budget and time constraints.
Let’s use the hiking boot example from earlier to show how inspection levels affect on-site testing. The table below shows various tests common for footwear that you might require for your boots and the sample size for each inspection option proposed.
Sample sizes range from zero pairs, to the special sampling level S1 (5 pairs for this lot size), to the general sampling level for the corresponding inspection option. Option 3 allows for the most tests to be performed on the largest sample of boots. While option 1, the “budget option”, allows for the fewest number of tests to be performed on the smallest sample of boots.
Having different options for testing gives you the flexibility to choose which tests are important for you and in what frequency. By suggesting common tests relevant for your product and working with you to choose an inspection and testing regimen for your product, AQF helps you get the greatest insight possible without overspending.
How AQF helps you prioritize inspection when and where you need it most
When to conduct QC inspection is an important consideration. Ideally, you could have an inspector at the factory daily, or almost daily, checking your goods throughout every production process. But most importers are limited by their budget in how often they can hire a third-party inspector. They’re often forced to choose the most critical among several key stages of production to inspect, including:
- Incoming quality control (IQC): Checking raw materials or components before production
- In-process quality control (IPQC): Checking semi-finished goods during production
- During production (DUPRO) inspection: Checking finished goods when 15-80 percent of the total order quantity is finished
- Pre-shipment inspection: Checking finished goods and packaging when 80 percent or more of the total order quantity is finished
Pre-shipment inspection is generally considered the bare minimum level of oversight suggested. But finding quality issues after production is mostly finished can leave you with few options for corrective action.
AQF works with you to plan inspections around your specific quality concerns and timeline.
For example, imagine you’re ordering a mechanical item with electrical motors which the factory has sourced separately from a sub-supplier. You’ve had issues with the electrical motors on previous orders and want to avoid repeat issues. But the motors are difficult to test once assembled into the final unit. Knowing your quality concerns for the motors and other constraints, AQF can suggest when to send an inspector to test the motors at an earlier stage prior to assembly.
How do travel costs add to your third-party inspection fees?
Aside from a usual man-day rate, third-party QC providers typically bill costs associated with the inspector traveling to and from the inspection site.
In large countries like China or India, travel costs can be significant if an inspector needs to travel great distances to different factories. In China, some public transportation options like the high speed rail network can make travel more efficient. But in less-developed countries, public transport options are often limited and unreliable.
Where public transportation is unavailable, inspectors will often need to hire a driver or taxi to take them to factories. And these costs can be quite significant over time. Even with factories in major manufacturing areas in China, it’s often more efficient to take a taxi from a subway station than to find a connecting public bus. And many cities have no subway system at all.
If your factory is located in a particularly remote location, you’ll likely face higher travel expenses for inspections.
AQF helps limit the travel expenses you pay
Working with AQF, you’ll benefit from an all-inclusive man-day rate for most inspections. Because expenses are factored into a flat rate, you won’t face added fees for travel on top of the quoted man-day rate. This means lower costs and greater clarity for you.
How can AQF offer competitive man-day rates with travel costs included? AQF has a wide network of inspectors based in various manufacturing zones internationally. With local inspectors based closer to your inspection site, you pay fewer travel costs.
For example, you might need an inspection at a factory in Ho Chi Minh City, Vietnam. Some QC providers may need to send an inspector from a distant city or from another country entirely if they don’t have staff based in Vietnam. You’d pay higher inspection costs as a result. But the travel cost of AQF inspecting in Ho Chi Minh City would be very low, since AQF has inspectors located there.
Conclusion
Cost isn’t the only factor in deciding between QC providers. But it’s certainly near the top of many importers’ concerns.
You can still get a clear report of the quality of your products before they ship without paying high inspection fees. AQF works with you to apply an inspection scope and testing regimen that fits your budget. You’ll save money with access to a wide network of inspectors to limit the travel expenses you pay for each inspection.
So when cost is a deciding factor in choosing a QC provider, don’t just look for the lowest possible man-day rate. Look for the QC provider that offers the greatest flexibility and best adapts to your budget without compromising on service.
How do you balance your inspection needs with your budget? Let us know in the comment section below!
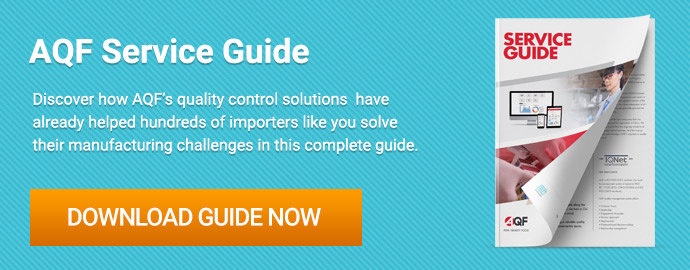