Imagine receiving two separate inspection reports for the same order but each showing different results. One shows the order passed inspection and there are only a few minor defects. The other shows a number of major defects and that the product failed a crucial on-site test.
Which report should you trust? Has the first inspector’s integrity been jeopardized?
Many importers have come to rely on third-party QC providers to provide this reporting (related: 4 Ways Importers Conduct Product Inspection [eBook]). Unfortunately, this has opened the door to corrupt and unethical practices by both factories and inspectors to skew inspection results in their favor without you, the importer, knowing.
How do you ensure integrity issues don’t affect your product QC? Before we get into at how Asia Quality Focus (AQF) prevents integrity problems, let’s take a look at some of the most common ways product QC can be derailed by corruption and how these problems directly impact your reporting.
What specific actions can trigger corruption in product QC?
You might be surprised by some of the behaviors that can trigger corruption in product inspection. Though some gestures from supplier staff are more direct, others are far subtler. There are a number of various perks supplier staff may offer an inspector that can compromise that inspector’s judgement, including:
- Cash bribes – in China and some Southeast Asian countries, suppliers may attempt to bribe an inspector outright, typically by offering a red envelope, or “hóng bāo” (红包) in Mandarin. Red envelopes normally contain money and are commonly exchanged among friends on special occasions.
- Packaged gifts – such as alcohol, tea, cigarettes or other small goods.
- Meals – inspectors are normally responsible for their own lunch, but factory staff sometimes offer to provide a meal.
- Invitations to after-service social activities – including dinner, karaoke or other social activities.
- Transportation – inspectors typically rely on public transportation to travel from their home or office to the inspection site. But factory managers sometimes offer to send a car for them, especially when the factory is located in a remote area.
- Accommodation – inspectors usually return home immediately after they complete inspection. But they will find local accommodation to stay overnight if the factory they’re visiting is far from home. Factory staff will sometimes offer to provide this accommodation.
Some of these may seem like innocuous, friendly gestures. But they’re often the first step by factory staff to building a rapport with the inspector. And as inspectors and factory staff become close, this relationship can make inspectors biased.
What are some symptoms of corruption in product inspection reporting?
There’s a reason for the adage, “don’t mix business with pleasure”. Over time, a close relationship between factory staff and your inspector can, and will, create conflicts of interest (related: Top 5 Issues that Can Affect QC Auditor Integrity).
Now that you understand the types of behaviors that can trigger corruption, let’s look at how these can affect the quality of reporting you receive for your products.
False reporting of product inspection results
One of the more obvious ways corruption can affect product QC is outright falsifying results. This can include cases where the inspector deliberately falsifies:
- The number of defects found in the sample. For example, let’s say your inspection result should be “fail” if the inspector finds six or more major defects in a sample of 80 units. While the inspector might find eight major defects, they may choose to report only five so that the inspection result is “pass”.
- The types of defects found in the sample. In the same example above, the inspector may choose to classify three major defects as minor to limit the number of major defects reported to within the maximum allowed. This is more likely to happen with certain defects, like surface scratches, which may be more difficult to classify objectively without actually seeing the defect first hand (related: How AQL Sampling Affects Your Product Inspection Results).
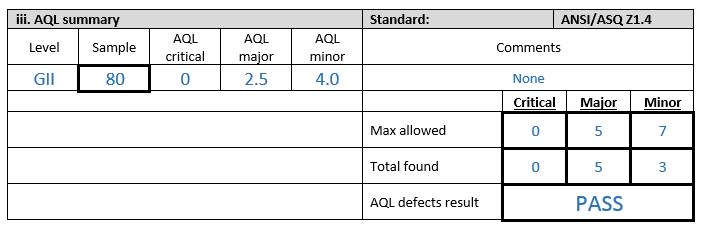
- On-site testing results, whether the inspector actually skipped the testing procedure, or the product failed the test. For example, a corrupted inspector may report that your product’s packaging was undamaged following a carton drop test. But in reality, the packaging was damaged, and factory staff didn’t want to have to replace packaging and repack the entire order.

Inspecting a smaller sample than agreed upon
Like most importers, you’ll probably want to determine what quantity of units from mass production, or sample size, to check prior to inspection. Sample size is an important consideration because:
- You’ll most likely be paying your inspector based on how much time they need to inspect. So the sample size inspected will impact your costs.
- The scope of inspection largely depends on how many units the inspector checks. The larger the sample size, the more insight you have into the quality and status of the goods.
If the inspector uses a smaller sample size than the one you’ve agreed to, you’re overpaying for a smaller inspection scope than you’d like. For example, although your report might show the inspector checked 125 units, they may only have checked 80. Even if the result was correctly marked “pass”, there’s a greater chance of that problems were overlooked because the inspector checked a smaller sample.
Overstating order status
Besides informing you of any product quality issues as early as possible, inspection helps you confirm whether your suppliers are on track to meet production and shipping deadlines. Inspectors provide transparency into what quantities of units are at various production stages by reporting on order status.
What could go wrong?
Let’s say you have a supplier in Foshan, China manufacturing an order of 20,000 floor lamps. You’re already behind schedule, but your Chinese supplier has promised they’ll be able to finish production by January 31st, leaving more than a 2-week window to ship the goods before the factory must close for Chinese New Year.
Concerned about your product quality and the status of production, you ask your third-party inspector to visit the factory and report back. But because your inspector has a close personal relationship with factory staff, she falsely reports that the order is 70 percent finished and packed. Little do you know, factory workers have only finished 20 percent of the order and haven’t packed any units.
What began as a big problem has now ballooned into a bigger one. Based on false information, you reassure your customers that they can expect to receive the goods on time. Then when the factory ultimately misses the shipping deadline, you may only hear about it from your freight forwarder. Or worse, your customers may contact you wondering where their products are (related: 3 Ways Product Inspection Helps Importers Meet Shipping Deadlines).
Sharing your confidential information with factories or consumers
When you hire a third-party QC provider, you’re also entrusting your intellectual property to them. Some manufacturers are highly secretive about their product releases until they’re ready to make them public. Take Apple, for instance. Even with their famously secretive policies, details of the iPhone X were leaked to the public prior to their official release.
In Apple’s mandatory filing to the U.S. Securities and Exchange Commission (SEC) in 2017, Apple noted:
Although the Company takes steps to secure confidential information that is provided to third parties, such measures may not be effective and losses or unauthorized access to or releases of confidential information may still occur, which could materially adversely affect the Company’s reputation, financial condition and operating results.
Your company may not be as large as Apple. But unauthorized sharing of your confidential information to your competitors or consumer base could be similarly disastrous to your bottom line. Some examples of inspector confidentiality breaches include:
- Taking your products from your supplier’s factory for their own personal use.
- Selling rejected goods with your company’s branding, which can be especially problematic if there are safety issues with your rejected product.
- Sharing your product design files and specifications with competing factories to produce a copycat product at a profit.
All these scenarios could harm your brand’s reputation and competitiveness in the market.
A word about product inspector extortion
It’s not surprising that factory staff might try to influence inspectors to falsely issue a report with a result of “pass”. But extortion on the part of inspectors is increasingly common. Rather than factory staff offering perks to your inspector in exchange for a positive report, you’re inspector might demand a “kickback”, or payment, in exchange for not submitting an negative report.
Like corruption, extortion can lead to a number of problems stemming from inaccurate reporting. But there are a number of steps AQF takes to help prevent either from occurring.
How AQF prevents integrity issues in quality control inspection
Any professional QC provider should have specific practices in place to prevent the integrity issues mentioned above. As one that’s provided inspection services since 2007, AQF has several strict policies to protect you and ensure your reports are as accurate and transparent as possible.
Hiring practices that encourage high integrity behavior
Encouraging high integrity starts with hiring the right people. When inspectors are financially secure and satisfied with the monetary return for their hard work, they’re much less likely to accept outside financial incentives like bribes. That’s why AQF offers competitive pay to our inspectors at or above the market average. In turn, our inspectors are more likely to remain independent and objective throughout the inspection process.
Integrity screening during the interview process
Some importers ask how we screen potential inspectors during the hiring process. One way our hiring managers assess a candidate’s integrity is by asking them to respond to integrity-focused questions and scenarios. A few questions we often ask include:
- What types of rewards or gratuities do you think it would be inappropriate for you to accept from factory staff?
- Has someone, other than an employer, ever offered you a reward in exchange for a certain result on the job? If so, how did you react?
- How do you think accepting a bribe would affect your ability to perform your job adequately?
Responses to questions like these help us assess an inspector’s experience and judgement with handling challenging situations. This gives you greater assurance that your inspectors can recognize any attempts at corruption and report them appropriately.
Code of Ethics addressing integrity of inspection staff
A standard Code of Ethics is a great place to remind employees of important values in any company. But AQF’s Code of Ethics includes more details about what we consider acceptable and unacceptable behavior in the field. For example, you’ll find that we prohibit several activities that could hinder inspector’s judgement, including:
- Socializing with factory or vendor staff outside of inspections, including but not limited to consumption of alcohol, KTV (karaoke), sight-seeing and any leisure activities outside of our normal realm of work
- The offering, giving or accepting of bribes in any form, including kickbacks on any portion of a contract payment
- Giving confidential data to any party outside of AQF except, as necessary, to the factories and consultants who are directly related to providing quality services to our clients
- Personal business transactions, including but not limited to, buying from, selling to, providing services for or working on behalf of the factory, vendor, client or supplier
The Code of Ethics also dictates that should the factory ever try to bribe our inspector with gifts or cash, they should immediately report it to management. If they fail to report the situation immediately, they’ll face disciplinary action. AQF also makes it abundantly clear that should we confirm a staff member accepted a bribe, AQF will terminate their employment immediately.
Integrity documentation and policies for QC inspectors
Another preventative measure that AQF takes with every service is submitting our Service Declaration form. This form must be filled out and signed by a factory representative at the end of every service. It helps confirm that factory staff didn’t provide any unauthorized benefits to your inspector, such as gifts, personal favors, accommodation, meals or transportation.
Even interactions that may be seen as “normal” or “common” in Chinese culture are discouraged, such as accepting a cigarette or meal from the factory. Policy dictates that if the factory provides lunch for an AQF employee (such as a takeout meal), the cost of the meal cannot exceed 50 RMB (about $7 USD) per AQF employee.
Rotating QC inspectors regularly
Even if factory staff don’t offer a bribe or other benefits to inspectors, they can still influence your reporting when the same inspector is visiting the factory repeatedly over several weeks or more. Rotating inspectors regularly is one of the best ways to prevent your any inspector from developing a personal relationship with factory staff.
Some importers will specifically request assigning same inspector for every factory visit. But we generally rotate inspectors to help keep them impartial and keep your reporting reliable.
Internal audits to monitor inspector conduct in the field
Even with the other practices mentioned above, it can still be difficult to confirm how your inspector is actually behaving at the factory during the service. That’s why inspection supervisors will often shadow inspectors in the field. We usually arrange this without notifying the inspector beforehand to ensure the supervisor is exposed to the natural interactions between the factory staff and the inspector.
Inspectors may behave differently with a supervisor present. But managers can review the reporting history for your products to find any discrepancies in inspection method or results that could point to integrity issues. For example, if your product narrowly passed the last five inspections and suddenly starts easily passing the next few with the same inspector, managers will consider potential reasons for the sudden improvement. And they’ll investigate further if results change after rotating inspectors.
Conclusion
As an importer, it’s hard to spot integrity issues during the product QC phase. This is especially true when using a low-budget QC provider that pays their staff less and isn’t as attentive to integrity issues. Inspectors may under-inspect, overstate production status or simply falsely report on your order. All of these can cause real problems for you and your customers.
AQF tackles these issues with clear policies, documentation and effective hiring practices to constantly monitor inspector conduct and prevent integrity problems.
The next time you’re considering hiring inspectors, make sure you pay attention to integrity, in addition to price. Choosing a QC provider that can’t give you concrete details about how it handles integrity issues can put your product quality and brand image in jeopardy.
Have you ever had to address an integrity issue with your inspectors? How did you proceed? Let us know in the comment section below!
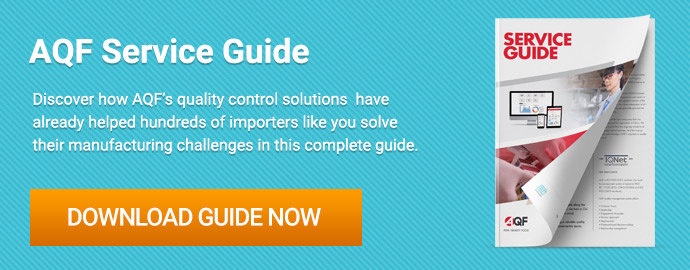