International importers buying from Asia are often asked to assure the quality of their goods: after all, importers must legally take full responsibility for the quality of their products to conform with safety, health and other national regulations. Their buyers also require good quality. However, many suppliers in Asia want to work independently, so the importer has to strike the right balance in the equation: quality assurance vs. quality control.
Definitions for quality assurance vs. quality control
Quality assurance (QA)
It is a proactive and continuous approach that puts in place systems, processes and actions to answer to specific needs. It includes the continuous improvement of the processes and the set up of a proper quality management system usually based on the ISO 9001 standard.
Quality control (QC)
It is a reactive approach that mainly focuses on the product or on what has been done. It allows to identify possible non conformities and set up corrective actions.
Quality control vs. quality assurance in the ideal Asian sourcing world
Traditionally, local suppliers manufacture products and international buyers purchase the goods and ship them to Western countries (that's a simplified overview of course, the reality is more complex).
In this context, the division of labour can be relatively simple:
- Quality assurance is done by the supplier: designing a good product, buying good components, adding and supervising reliable production processes and continuously checking and improving both to avoid any defects. Internal quality control is part of the process.
- Quality control is done by the buyer: there are a wide range of quality control solutions however the most common one in the consumer goods industry is the pre-shipment inspection performed by a third party quality control company. It serves to double check that the quality assurance was successful, thus if the goods are conformed to the buyer's requirements.
Buyer's quality control needs while purchasing in China
As a matter of fact, China suppliers limit investments in quality assurance and prefer the buyer covers costs of quality control and quality assurance. Therefore the buyer should take into consideration other quality control solutions prior to the pre-shipment inspection such as:
1. Reactive quality control right after the order confirmation and during the whole production process to help suppliers to assure quality and respect the product specifications required. It includes the raw material inspection, first article inspection, during production inspection, pre-shipment inspection as well as production monitoring.
2. Pro-active quality assurance prior to the production, by performing factory audit and corrective action plan. When choosing this option, buyers clearly enter into the quality assurance process.
Quality Assurance and Quality Control are both done by Buyer and Supplier. Factories do perform quality control (even limited), and buyers do support on the quality assurance by setting up clear specs or performing factory audit for example.
And you: When looking at quality assurance vs. quality control, what is your preference to secure your imports? Contact our expert to help you out!
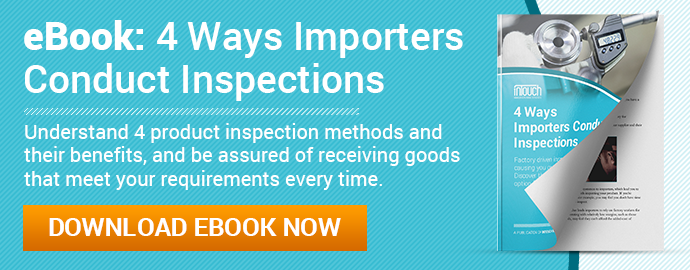