Research shows it takes consumers just 7 seconds to form a first impression about your product.
Imagine if your factory made a crucial error in the retail packaging and misspelled the name of your product. Not a good first impression, right? Worse still, imagine if your product was damaged during transit and didn’t even make it to the retail shelf because your supplier’s factory didn’t ship it with the proper protective packaging.
Damaged or defective products can be a major drain on your company’s profits when they’re unsellable. Packaging inspection before shipping is vital to catching defects related to packaging and ensuring your products reach their destination on time and in the best condition (related: Packaging Inspection Guideline [eBook]).
Importers often check both product and packaging at the same time during final inspection. Final inspection occurs when 80 percent or more of the total quantity of goods is finished and packed. But some importers may opt to inspect the packaging on its own at their packaging supplier's facility, often when they have special or unique retail packaging requirements.
So what issues should you or your inspector look for during packaging inspection? Let’s take a look at the three most common defects found during product inspection, their consequences and what you can do to fix them.
1. Incorrect or missing shipping markings and barcodes
You probably have specific requirements for labeling your packaging with appropriate markings and barcodes. Logistics companies, customs officials and warehouse staff all use this information to efficiently ship your products from their country of origin to the hands of your end consumers. And you could face customs delays or outright refusal from distributors to stock your goods if your packaging is mislabeled.
Don’t assume the factories supplying your products and packaging clearly understand your own labeling preferences. Shipping marks and labels are requirements your suppliers need to have upfront, well before mass production begins. Perhaps more important than your own preferences, you may also need to follow specific labeling requirements set by your retailer for processing at their warehouse or distribution center.
Markings generally include:
- Purchaser’s name
- Purchase order (PO) number
- Item number and description
- Carton dimensions and weight
- Number of carton within set (1 of 20, 2 of 20, etc.)
- Country of origin in compliance with international requirements, as well as country of destination
- Any appropriate warning labels and icons (e.g. “fragile” or “this side up”)
Shipping marks can either be printed directly on the carton, printed on a label, or in some cases, like the outermost shipping carton number, handwritten. Some of this information can also be contained in a barcode, or even an RFID tag.
Some issues with shipping marks and barcodes are classified as critical defects. Critical defects are generally serious enough to result in failing inspection and rejecting an order. Many importers will ask their supplier to change the affected packaging for the entire order if inspectors find even a single critical defect (related: How AQL Sampling Affects Your Product Inspection Results).
How can you prevent and address incorrect or missing shipping markings?
Preventing quality defects is almost always easier and less expensive than trying to correct them after they’re already present (related: How Experienced Importers Limit Product Defects in 3 Stages [eBook]). And one of the best ways to prevent issues related to packaging barcodes and markings is to send your suppliers a QC checklist that includes a clear packaging standard and artwork requirements to follow (related: 5 Essentials of a QC Checklist [eBook]).
But even when you’ve provided clear requirements upfront, you’ll usually need a final inspection before shipping to confirm factory workers actually followed your packaging standard correctly. Especially when you have multiple SKUs within the same order, you might find that factory workers can easily make mistakes with assigning the correct information. Final inspection represents one of your last chances to verify products and packaging before they leave the factory.
Professional, third-party inspectors will typically check shipping marks against your provided requirements using a QC checklist. They’ll also carry a handheld barcode scanner to scan barcodes and check them against your specified barcode numbers. If you’re using AQL for inspection, your QC checklist might include the following defect classifications related to shipping marks and barcodes:
Corrective action for mislabeled packaging may be as easy as asking your supplier to replace an incorrect label with a new one. But they might need to replace the carton itself if incorrect shipping marks are printed on the carton. Addressing mislabeled packaging can sometimes lead to shipping delays, especially when corrective action needs to happen at a facility different from the one where inspection took place.
2. Incorrect packing method
Imagine you’re importing delicate ceramic bowls from your factory in Guangdong, China and shipping them directly to an Amazon warehouse for distribution. One day you get a call from your distribution contact who tells you most of the bowls were cracked and chipped on delivery. You later discover the bowls were damaged during shipping because factory workers packed them incorrectly in their cartons.
This example shows the importance of ensuring your suppliers handle your products with care and pack them according to your requirements before shipping. But packing method isn’t just important for protecting fragile products like ceramics or glass. Assortment can also greatly impact the cost you pay for freight and packaging materials.
An incorrect packing method can involve a number of issues, including:
- Using the wrong packaging material
- Incorrect packing assortment
- Missing or incorrect cushioning material, or plug, for adequate protection
- Using the wrong carton size, leaving extra space inside of the carton, which leads to movement of the product that can damage it
- Paperboard missing or upside down
Any of the above issues are typically classified as major defects when using AQL for inspection. Major defects are often serious enough to lead to customer returns and can result in an order failing pre-shipment inspection if found in high quantities (related: 3 Types of Quality Defects in Different Products).
In the case of many of these defects, like issues with cushioning material or paperboard, improper packaging can damage the product. Common issues with packaging material found during inspection can range from using the wrong thickness of polybag to the wrong ply cardboard. Other issues, like incorrect packing assortment, could affect your inventory or make it difficult to sell a product if a critical component is missing.
Another potential issue is higher transportation costs or product damage due to factory workers packing your products in incorrectly sized cartons. Oversized cartons take up more space in shipping containers, which can affect your cost. And if there’s extra space within the carton, the product might move around during shipping, which can result in damage.
How can you address incorrect packaging assortment?
If you’re facing problems related to poor quality packaging materials, this might be your supplier’s attempt to cut costs. And your supplier might opt for a lower quality material if you haven’t clearly specified the packaging materials you’d like the factory to use for your product. Provide your suppliers with a detailed QC checklist before production that includes your requirements for packaging assortment and materials. You can also ask your supplier to provide a sample of packaging and photos of the packing method for your review.
As with verifying other requirements, insist on inspecting the product and packaging before shipping. If the factory didn’t have the correct packaging materials in the first place, it could take additional days to order these materials from their sub-suppliers. But this delay is often worthwhile if it means your products will be shipped in the correct packaging.
3. Incorrect spelling, wording or graphics on retail packaging
Many importers invest significant time and money to design retail packaging that customers will find appealing. Some would even argue that the quality of retail packaging is almost as important in making a sale as the quality of the product itself. High quality and customized packaging can make your product appeal to premium buyers. Customers today even share videos on social media of them unpacking, or “unboxing”, new products, especially high-tech consumer products or premium fashion products.
Incorrect retail packaging can make your product difficult to sell to the end customer due to misunderstanding or misrepresentation of your brand. Common issues found in packaging inspection can include:
- Missing, incorrect or illegible wording
- Missing, incorrect or illegible graphics
- Color deviation within the packaging
- Color deviation from approved sample
An issue in retail packaging often affects the entire order due to mass printing processes. You might consider less serious issues that don’t affect your product’s salability to be minor defects within your quality tolerance. Whereas more serious issues that affect all or most of your order might be major or critical defects that require your supplier to replace retail packaging.
Inspectors typically check retail packaging against a golden sample and branding text and digital files provided by the importer. To check the color of graphics, inspectors will compare colors found in production with specified colors shown in a standardized Pantone color booklet. Color requirements are especially important where company logos are concerned.
How can you avoid packaging defects related to wording or graphics?
Most retail packaging issues can be avoided by providing suppliers with clear requirements upfront. Any serious issues found during inspection of retail packaging might require reprinting of all or most of the affected retail packaging materials. The following steps can help you avoid a mistake in retail packaging from appearing in mass in your finished products:
- Ask your supplier to send you the printing file for review before mass printing
- Ask your supplier to send you packaging samples for approval before mass printing (these will also be helpful later during inspection)
- Check packaging against a golden sample during pre-shipment inspection
Most product inspectors won’t be native speakers of your language, unless you’re personally inspecting the product yourself or sending a representative from your company (related: Why Most Importers Don’t Conduct Product Inspection Themselves). So it’s vital that your inspectors fully understand all of your packaging requirements. Communicate with your inspection staff ahead of inspection so they don’t have to rely on their own judgement in assessing the quality of your packaging.
It’s up to you as the importer to consider what effect a retail packaging issue will have on your ability to sell your product. For instance, a typo in your company or product’s name is likely more significant than a subtler typo in a product’s instruction manual. Likewise, a small difference in the shade of green used in your logo is probably less problematic than use of a completely different color, like purple.
You’re the best judge of what your customers expect of you. A careful review of remarks and photos in your inspection report will help you determine if your product’s retail packaging will meet these expectations or fall short.
Conclusion
These are the three most common defects you might find during packaging inspection, but there are others. And the defects you find will likely vary based on your product type. Small consumer products for retail are often packaged in blister packs, while garments are almost always packaged in polybags. Some small industrial components may not be individually packaged at all, but rather packed together in boxes by the tens or hundreds.
Regardless of your product type, an inspection should be comprehensive enough to include checks of all applicable retail packaging, polybags, inner cartons and master cartons. Otherwise, you might find yourself in danger of product damage, shipment delays or even unsellable goods – an importer’s worst nightmare.
What other quality issues have you found with product packaging? Tell us in the comment section below!
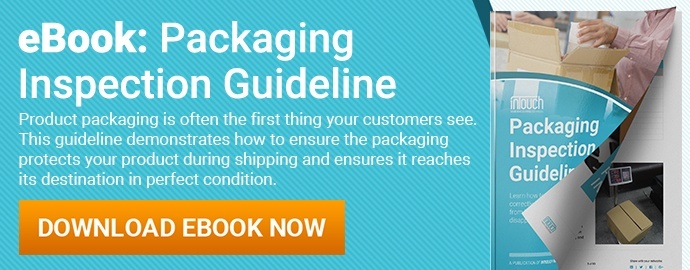