In today’s competitive markets, customers have increasing expectations across all industries. Product quality standards and rollout deadlines have to be consistently met in order to keep customers satisfied. For automotive companies, it is important to have proper quality planning methods in place in different phases of development, from early market tests to production inspections.
In this post, we will examine five advanced methods that have been successfully adopted by the industry.
What Is APQP?
Advanced product quality planning (APQP) was invented by Ford, General Motors, and Chrysler in the late 1980s. The “Big 3” wanted to streamline production lines and elevate product quality levels to meet customer expectations.
The APQP process concerns all components and subsystems of a product. It simplifies product planning because it uses methods to distill the critical product requirements that need to be met to maintain conformity. By centrally managing product quality throughout the supply chain, errors during line production can be prevented.
But it is not only about the product; APQP also addresses non-tangible aspects such as operator expertise, manufacturing locations, craftsmanship levels, prototypes, and packaging. These have to be ticked off as well before production can start.
1. Risk Assessment
A mature organization needs to be proactive in judging where in the process setbacks can occur. Product quality is not only the result of strategic product development and process management but potential risks must also be managed.
For automotive parts, quality can best be ensured by reviewing where flaws can happen beforehand. In APQP, risks can be managed with failure mode and effects analysis (FMEA).
In FMEA, as many components as possible are reviewed before production or prototyping begins, so all possible failures and their causes and effects can be identified. A 5-10% scrap rate is typical, but with good risk assessment, the error margin can be reduced by several percent. This way, quality control is not just an afterthought.
It is also important to estimate whether contract manufacturers and other third-party suppliers can produce and test to meet compliance standards such as UL, CE, ROHS, and FDA, quality standards established within your own company, and aesthetic color, material, finish (CMF) specifications.
Preventing future revisions at an early stage means saving a bulk of costs. It is equally important to agree on mold standards, especially if you are looking to hand over the mold to a factory abroad when scaling up at a later stage. A factory visit can give you valuable insights, such as:
- A feel for the company culture and work environment.
- The opportunity to evaluate machinery, product samples, and storage conditions.
- An idea of how much prices can be negotiated, how they will prioritize your project, and whether or not you are granted access to upper management.
2. Set Up a Thorough Quality Control Process
Quality control (QC) sets up checkpoints to allow for corrective measures in the design and production process. It concerns design features, materials, tolerancing, CMF, and surface treatments such as corrosion resistance and clearcoat adhesion.
Product specifications outlined in a product requirement document (PRD) are converted into a QC checklist to check samples against all product requirements. This is ideally done in all phases, from the “alpha” proof of concept (POC) prototype to the “beta” engineering prototype, production samples, and the full commercial product during production testing, mass production, and ramp-up stages.
It is ever-more important to validate not only functional requirements but also those voiced by the customer (VOC). The point is that product quality is not only meant to prevent repairs and meet its projected end of life. The customer’s definition of “quality” is more complicated, so it must fit the way the end-user wants the product to look and how they want it to function.
Conveying the voice of the customer through engineering and production can be challenging. There is a balance between what the manufacturer can do and what the customer wants, and in today’s competitive environment the scales are tipping toward the latter.
To test such “soft” customer requirements, it is paramount to establish a working relationship with lead users and involve them in different stages of the process for interviews or focus groups, exploratory user tests, field analysis, and after-sales feedback where possible.
These loops will complicate the development process in that requirements are continuously changing. It requires non-linear agile workflows like Scrum or Kanban. Quality function deployment (QFD) is a useful tool to simplify complexity by prioritizing customer requirements and strategizing how to tackle them.
It results in a chart called the house of quality (HOQ) that lists all the relevant customer attributes (CAs). For example, CAs for a car door may include:
- It shouldn’t rust.
- It should make a pleasant sound when closing.
- The handle should be easy to use.
These often 100+ CAs are then related to ways the company can ensure quality requirements will be met.
For quick market feedback, customer preferences can be probed by showing them images of different concept designs together with a questionnaire. Use Likert scales to ask to what degree customers agree or disagree with statements about the different designs.
This hardware form of A/B testing is a quick method for brands to get to understand their crowd. In later stages, engineers will build a minimum viable prototype (MVP) of the new vehicle using low-cost techniques and 3D printed parts to evaluate the driving experience or interactive features.
For marketing and sales purposes, consider creating a virtual showroom for simulated shopping tests. Such validation tests are crucial to a value-based sales methodology.
3. Statistical Process Control
Statistical process control (SPC) uses sensor and measurement data for risk management to minimize scrap rates and ensure the stability of the manufacturing process. Ongoing monitoring of the production process results in control charts that can verify the success metrics.
Measurements are made over a defined period in the areas known as 5M&E:
- Man
- Machine
- Material
- Method
- Movement
- Environment
This helps to prevent rather than correct defects, accidents, and losses—and in particular, it is effective in detecting “special” sources of variation in the process that often prove to be critical bottlenecks for efficiency.
Excessive variations can happen in any of the 5M&E areas, for example:
- Part wear rates.
- Polymers leaking volatiles.
- Jigs and fixtures getting jammed.
- Untrained staff.
A herringbone diagram is an easy tool to identify cause-and-effect relationships by mapping possible sources of a problem. Another way to find the most important conditions that affect variation is by doing experiments (DOE).
Measurements systems analysis (MSA) is the field that teaches how to set up reliable and replicable experiments using proper measuring instruments, test methods, and statistical analyses.
4. Production Part Approval Process
Product part approval process (PPAP) is a methodology that involves making a production control plan and then measuring produced parts against their requirements for dimensions and performance. Based on this, a change in the manufacturing process, part design, or materials, can be necessary for meeting quoted production rates and part quality.
The final documented result is a “PPAP package” that is signed by the supplier and customer for mutual agreement before production can kick-off.
It is very important to discuss CAD models and prototypes and share Grasshopper files with vendors beforehand to verify that they can meet the original manufacturing plans and understand the most important design features. This prevents things like substandard materials and pivotal design changes on the part of the manufacturer.
Monitoring suppliers and subcontractors along the way are critical to ensure quality. The earlier feedback loops are built-in, the faster they will accelerate product development by finding fruitful areas of improvement, such as:
- Weight reduction.
- Higher production speeds.
- Reduced material consumption.
5. Theory of Constraints
Where SPC is quantitative and all-encompassing, the theory of constraints (TOC) focuses only on the most critical variations that take up the most resources. In this survey of industry leaders, 68% said improving supply chain resilience and agility is their top priority for 2021.
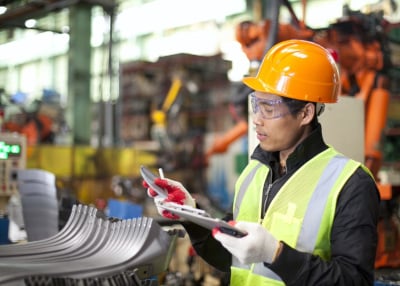
A chain is as strong as its weakest link, and by finding these TOC ensures that leaps in overall quality can be made. A rule of thumb is that eliminating the upper 20% of most impactful bottlenecks can improve quality by 80%.
Many causes of constraint will be answered by straightforward solutions such as improved expertise, new equipment, or standardization. Another way to deal with bottlenecks in processes is to put them first or last in the pipeline, or even separate them entirely.
For example, if custom or high-performance parts slow down the production line, they can be outsourced to their own department or another company. If one of the suppliers has a delaying effect, consider compacting the supply chain by selecting partners that can deliver most components as listed in the bill of materials (BOM). And to save on shipping resources, train freight is an attractive alternative to the ocean or air freight.
Automation is another strategy to improve consistency, throughput, and product quality. Robots take over labor-intensive and unergonomic tasks such as welding, sheet metal fabrication, general assembly, part transfer, painting, part finishing, and fabric trimming.
Machine learning augments advanced imaging techniques for product analyses, such as checking for imprecisions outside tolerance limits, missing components, errors in parts or assemblies, cleanliness, and damages.
3D printing, CNC machining, and injection molding can be used to create jigs and fixtures for assembly and testing purposes, customizable parts, or reduce part count by combining functionalities in a complex cutting-edge design.
Each new intervention needs to be critically analyzed to evaluate if the benefit is worth the investment or if the new process adds new selling points to the product.
The Winning Blend
We have discussed five ways of improving product quality that has stood the test of time in the automotive industry. The methodologies can be intimidating, but they have overlapping parts and become better understandable with increasing experience.
It is important to keep overseeing the different processes and learning in an environment that promotes continuous improvement and a zero-defect mindset. By combining tools and techniques, qualitative or quantitative, linear or agile, the right fit for your process can be made. This will result in a system that helps you overcome obstacles quickly and create a more steady workflow with great quality and throughput rates.
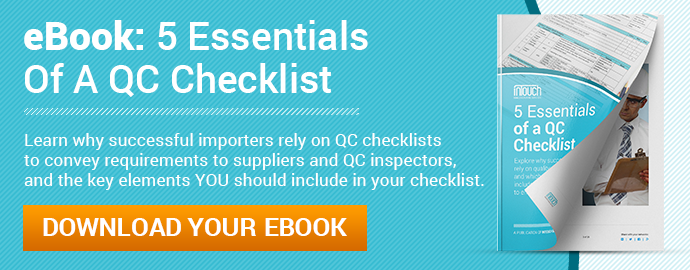