Experienced buyers recognize the benefits of pre-shipment inspection. It can help you catch mistakes before they leave the factory, help suppliers recognize areas for improvement, and help keep your product quality high. Most importantly, pre-shipment inspection helps you avoid extra costs (like product rework) you might otherwise incur.
But product inspections do cost money. And their costs can add up quickly. For most buyers, these costs are low relative to their purchase order. But for others, the costs are higher than they need to be.
Product inspection is a fundamental safeguard to verify goods before shipping. And there’s no reason why any importer should forgo inspection due to budget constraints. By learning these five reasons for high product inspection costs, you can verify the quality of your products before they leave the factory without paying a small fortune:
1. Similar SKUs are inspected separately
A common reason for high product inspection costs is that similar stock keeping units (SKUs) are inspected separately, rather than merged together. Merging SKUs allows for pulling one sample of two or more SKUs, instead of separate samples for each. This means that less time is spent pulling samples, inspecting and reporting. And since third-party inspectors typically bill based on time, time savings often lead to cost savings.
Say you’re sourcing 12 different styles of ceramic mugs from a factory in China. All the cups are created from the same mold and only differ in color. By not merging SKU’s, your inspector is basically treating them as different products. This method can result in your inspector taking longer to do the job because it:
- Needlessly increases the total number of pieces inspected and
- May require that any on-site tests for porcelain be conducted on a sample of each SKU.
If your inspection costs seem higher than necessary, take a look at the way your inspector is sampling SKUs. It often helps to merge SKUs that are similar.
When not to merge SKUs for product inspection
Merging similar SKUs is one way to prevent high product inspection costs. But merging SKUs is highly discouraged when the SKUs in question are not similar. Dissimilar products involve different production processes, so the inspection result of one SKU isn’t likely to reflect that of a different one.
For example, let’s say you’re sourcing six SKUs of ceramic mugs and six SKUs of promotional bar glasses from the same factory. The processes used for manufacturing the bar glasses will differ significantly from those used for manufacturing the ceramic mugs. So rather than inspecting all 12 SKUs together, it would be better to inspect the mugs and glasses separately (related: When Should You Combine SKUs for Product Inspection?).
"Considering merging SKUs doesn't hurt. Just make sure you know when to actually do it. #mfg"2. Re-inspections with limited improvement
Product inspection can be beneficial on multiple fronts—verifying an order of goods for an importer and pointing out areas of improvement to a supplier. Still, some importers and suppliers may not be realizing the value that they should. And another possible reason for high product inspection costs is repeat inspections of the same product with little or no quality improvement.
For example, you may be importing high-end ladies' dresses from a supplier in Vietnam. An initial inspection reveals open seams and other garment defects on a high number of inspected pieces. So you communicate the issues to your supplier and schedule a follow-up inspection. But the second inspection finds the same issues reported last time haven’t been addressed by the factory. The goods need to be reworked by factory staff and then re-inspected before they can ship.
What can you do?
Set clear product expectations upfront
Sometimes a supplier simply doesn’t value a particular customer enough to conform to strict product requirements. But often quality defects and other problems can occur simply because the supplier didn’t clearly understand the customer’s expectations. Here are a few key ways to make sure you and your supplier are on thhttp://www.intouch-quality.com/blog/quality-control-inspection-checklists-and-how-to-use-them/e same page:
- Know how to effectively communicate with overseas suppliers to ensure your messages are heard and not misinterpreted.
- Issue a thorough purchase order (PO) that addresses your expectations.
- Create and maintain a detailed QC inspection checklist that includes various product requirements like dimensional tolerances and which quality defects are unacceptable.
When it comes to product requirements, preventing issues is generally easier and less costly than trying to correct them as they occur.
Chargeback the supplier for any subsequent product inspections
If your supplier fully understands your expectations and the goods still don’t pass inspection, it may be time to enforce a penalty, such as charging them for repeat inspections. Asking the supplier to pay for needless re-inspections of nonconforming product often serves as an incentive for improvement and can offset high product inspection costs.
But not every importer will be able to successfully chargeback their supplier for inspections. Importers that have just started working with a supplier or buy small quantities of product will likely find it difficult to enforce a chargeback to their supplier. In fact, asking a supplier to cover the cost of inspections can actually hurt your relationship with that supplier, especially if you don’t have a long-standing relationship with them (related: 3 Tips for Stronger Supplier Relationships).
If quality problems or other product issues persist from one inspection to another and chargebacks aren’t a feasible option, it may be best to look for another supplier that’s more cooperative.
3. Long travel time for inspectors
Whether you’re working with a third-party inspection (TPI) company or have your own staff visiting a factory to inspect, travel time for inspectors can be a major cost (related: Independent Inspection vs. In-House Inspection). Importers often overlook just how much factory location and distance from the nearest available inspector can affect their overall QC costs.
Here are several costs, typically incurred by importers, which depend heavily on factory location:
- Bus, train, taxi fare and/or flight tickets;
- Accommodation in cases where an inspector needs to travel a great distance to the inspection site and will stay overnight someplace locally;
- Wages paid to inspection staff for their time in transit; and
- Any meals the inspector eats during their time.
It’s easy to see how travel time for inspectors can contribute a lot to high product inspection costs. For example, you may need an order inspected at a factory in China’s northern Hebei Province but only have inspectors in the southern region of Guangdong Province. In this situation you’d likely be paying a lot more for travel expenses on top of what you’re already paying for wages or salary.
Even if you’re working with a TPI that’s billing you at an all-inclusive man-day rate—as many TPIs do—that rate will probably be high relative to one where inspectors are based closer to the inspection site.
Inspect locally to avoid high travel expenses
As shown above, one reason for high product inspection costs is often high travel expenses. It can be very expensive to have an inspector travel an unnecessarily long distance to a factory for inspection. A more cost-effective and efficient way to inspect is to hire locally based staff to inspect in their locality. Generally, the closer the inspector is to the inspection site, the lower their travel expenses will be.
Maintaining local staff for in-house inspections
Professional QC companies often rely on hiring local inspectors in order to limit their expenses and offer their clients more competitive rates. As an importer, you can approach QC with the same principle in mind. Some importers have in-house staff that travel vast distances between cities—even countries—to inspect orders before they ship. These same importers can avoid high travel costs simply by hiring staff closer to the inspection site.
Supplementing in-house staff with local third-party inspectors
Other importers may feel they don’t require inspection at a particular area frequently enough to warrant hiring a local inspector. A recommended solution here is to hire a third-party that does have local staff in that area. Importers can avoid high travel costs for these areas where inspection is needed less often by supplementing their QC efforts with third-party staff.
"An #inspection will typically be cheaper if it uses local people to conduct it"4. Inefficient sampling during inspection
Where product inspection is concerned, the acceptable quality levels (AQL) standard is widely regarded as the industry standard. AQL makes the inspection process more objective by showing how many minor, major and critical defects should be allowed in a particular sample size at a particular tolerance level. Inspections using AQL typically have a “PASS” or “FAIL” result, which helps the importer decide whether or not to approve the order for shipping.
But for AQL to be used for inspection, the inspector must pull sample sizes of each SKU that conform to the AQL standard. Pulling particular sample sizes of each SKU often increases time spent during inspection and generally decreases the total number of pieces checked. So some importers choose to forgo using AQL when met with high product inspection costs.
Inspections based on time
Let’s say you’re importing watches from a factory in Taiwan. The order quantity is relatively small, with just one SKU of 1,000 pieces. If your inspector uses AQL, the sample size matching the highest general inspection level is only 125 pieces. That means they’ll stop inspecting once they’ve checked 125 pieces, even if they have plenty of time to check more. With most TPIs, you’ll be paying at least one man-day for this service whether the inspector is in the factory for the full day or not.
But rather than relying on the AQL standard, you might ask the inspector to inspect based on time. Here the inspector isn’t limited to checking only 125 pieces. They may be able to reasonably check 175 pieces and report on the quality in the same amount of time. Now you’re able to see the inspection results of 40 percent more pieces than if you’d used AQL—and at no added cost.
Negative effects of inspecting based on time
Opting to inspect based on time, rather than AQL, can help you avoid high product inspection costs. But it’s also worth noting that there are some disadvantages. Since the AQL standard yields results that are statistically significant, it’s often more difficult to interpret the results of an inspection that doesn’t use AQL.
How many minor or major defects is too many? On how many pieces should on-site testing be performed? These are questions that make it difficult to arrive at a straightforward “PASS” or “FAIL” result. Likewise, it also makes it more difficult for your supplier to understand your tolerances for quality defects and other issues without being able to refer to the AQL standard. These are consequences that each importer should consider before forgoing AQL for inspection.
5. High AQL sample sizes
If an importer chooses to use AQL for inspection, they’ll typically have to decide on an appropriate sample size for each inspected lot or SKU. Since larger sample sizes usually require more time to inspect, they also tend to be more costly. And high AQL costs are a fifth factor for high product inspection costs overall.
Let’s say you’re importing hardwood furniture from a supplier in Vietnam. Your order is made up of two SKUs—60 tables and 120 chairs. At these quantities, the SKU of tables falls into the lot size range of “51 to 90” and the SKU of chairs into the range of “91 to 150” on the AQL chart. Based on general inspection levels “I”, “II” and “III”, you have sample size letters “C”, “E” and “F” to choose from for the tables. And you have sample size letters “D”, “F” and “G” as options for the chairs.
On the other side of the AQL chart, you find these sample size letters correspond to “5”, “13” and “20” pieces for the tables and “8”, “20” and “32” pieces for the chairs. Let’s assume that inspecting the highest sample sizes—20 tables and 32 chairs—will take 2 full days. And inspecting the middle sample sizes—13 tables and 20 chairs—can be done in a single day. Choosing these middle sample sizes will help limit your inspection costs.
The consequences of inspecting smaller sample sizes
It should be clear that more time needed for inspection will increase inspection costs. And inspecting a smaller AQL sample can help to control costs by shortening inspection time. But just as there are consequences of forgoing AQL altogether, there’s also a consequence of lowering the sample size for inspection.
Simply put, a smaller sample size means a smaller inspection scope. You can’t be as confident about the status and condition of an order of goods looking at fewer pieces than you can looking at more pieces. So when you’ve finished inspecting a sample of just eight chairs out of a total 120 in your order—just 6.6 percent—it can be difficult to make an intelligent shipping decision. And that’s why it’s important to balance the scope of inspection with your individual budget.
Conclusion
For all too many importers, cost is a factor that can interfere with receiving a quality product. Many importers know that they have to be careful not to be too aggressive with negotiating with suppliers on price, which can lead to quality problems (related: Top 5 Tips for Negotiating with Chinese Factories). But some importers don’t realize that letting price get in the way of pre-shipment inspection can be equally detrimental.
There’s no reason why you can’t avoid high product inspection costs and still get the quality assurance you need before shipping. That’s why it truly does pay to know these five common reasons for high costs and what you can do to limit them.
And don’t miss the manufacturing podcast episode that covers this article!
Do you know any other reasons why some importers are paying too much for inspections? Share them in the comments below!
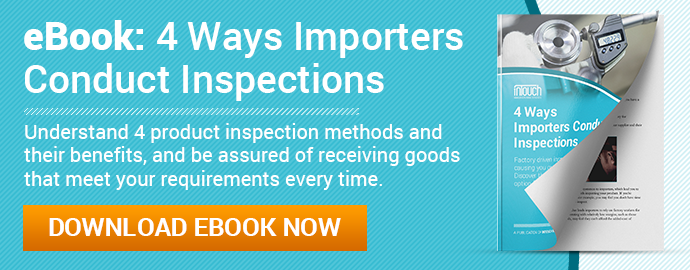