Best in Manufacturing – October 15, 2017
Each Sunday, we publish a list of top articles and other content related to manufacturing in areas like quality control, product development, supply chain management, sourcing, auditing and law.
1. Improve your margins with these tips for better manufacturing cost control
I’m a firm believer in the maxim, “you get what you pay for.” When it comes to product quality, if you decide to bargain to a rock bottom price, that’s what you’ll get – rock bottom quality. Yet that’s not to say if you pay an exorbitant amount of money, a great product is guaranteed. Cost management is still necessary.
This featured article, thankfully, offers insights to keep product costs low.
- Understand the factors affecting your costs: it’s hard to reduce costs if you’re not sure of all the factors influencing them. Identify each factor and understand its role in production to see if there’s a chance to save money.
- Develop a plan for cost management: once you get to the final version of your product, you might’ve already bypassed certain opportunities to avoid certain costs. By planning right from the start how to allocate money, you can achieve better savings.
- Use design-to-value: this approach for cost management identifies the product features that provide the greatest value for your customers and assists in your efforts to maintain that value while reducing costs.
- Use design-to-cost: this approach for cost management considers known inputs and projections of “short-term (supply chain) fixes” to determine an unchangeable cost parameter that a product must meet.
In a fantasy land of business, cost reductions wouldn’t be necessary. Business owners could simply throw money at problems until they disappear. But that’s not how the real world works – attention to costs is always necessary. And without an effective cost management strategy in place, your competitors might gain a leg up on you.
A few highlights from this featured article are reproduced above. To get the full scoop about cost management and how it can be used in manufacturing, check out the full article in the link below:
Manufacturing Money: Strategies for Cost Management – Aaron Continelli, BOSS Magazine
2. Pizza and supply chains: what do they have in common?
Let’s say you’re hungry at a restaurant and want a pizza. You expect to pay for it and get it in 25 minutes. What if, instead, the restaurant told you there’s a lead time of 3 weeks for giving you that pizza? In 3 weeks, you might still want the pizza, or your needs might change completely.
Just like this pizza example, if you have to wait too long for your product, it might not be what you really need by the time you receive it. Customers might not be “hungry” for it anymore. And worse, you might’ve ordered a great deal of product, only for it to be unwanted and unsellable by the time it arrives.
While reducing lead times might seem like an impossible issue to tackle, the author of this featured article provides a few steps to shorten them and hopefully help you get your products faster, when they’re still in demand. The author recommends the following:
- Form a cross-functional team: a supply chain is composed of many parts. Incorporating insights from members of different parts of it can help you learn where to improve.
- Define the value stream: where do your raw materials come from? What about other value-adding components? Find out their origins so you have a complete picture of your value stream.
- Map the current state: how does the product flow from beginning to you, the end point?
- Design the future state: in an improved version of your supply chain, what waste/inefficiencies would you remove from your current state?
- Develop an action plan: how are you going to act on the lead time issues you’ve identified?
No one wants to wait 3 weeks for pizza if they’re hungry now. Similarly, you and your customers are unlikely to put up with a long wait for your product. They might simply not buy what you’re offering, or worse, they might go to a competitor.
Learn about some of the factors that make supply chain lead times long, improvements that reduce lead time and more by checking out the full featured article in the link below:
Reduce Lead Time in Your Global Supply Chain with Lean Thinking – Tim McLean, Material Handling & Logistics
3. Where has Industrial Internet of Things worked in practice?
Like many in the manufacturing space, you’ve probably been hit with a seemingly endless stream of news about innovations with industrial internet of things (IIoT) over the last couple years. Sensory technology, cloud computing, real-time data analysis and virtual or augmented reality all promise great payoffs for manufacturers in theory.
But how have these innovations served manufacturers in practice? In a recent article published on IndustryWeek, Matt LaWell delves into some example of IIoT practices that have improved productivity and profitability.
Digital technologies to rebuild engines with greater efficiency
General Electric has invested $200 million to convert a food packaging plant in Pennsylvania into a remanufacturing plant for locomotive engines. According to Jamie Miller, the company’s CFO, the plant has raised productivity by integrating production with existing digital consumer technologies workers are comfortable using in their daily life.
Workers previously needed to completely disassemble an engine to find which parts needed repair or replacement. But now, Miller says,
…when that engine comes in the door, we already know the wear and tear on each component in that engine. We know which ones need heavy work scopes and really serious repair.
This difference translates to a reduction in unplanned downtime of 80-90 percent.
Tips for adopting IIoT technologies
Aside from cases where companies have successfully employed IIoT, the author summarizes a few “lessons learned” or tips from those at the companies themselves, including:
- Involve the right people: Successful companies noted the importance of including relevant staff in the planning and implementation of new technologies, with as little involvement from management as possible.
- Get started quickly and experiment: Often the consequences of inaction outweigh the potential consequences of problems with the technology itself. Companies that experimented with IIoT found it best to just get started trying the technology and addressing any problems as they came.
- Don’t be afraid to fail and make changes: According to John Carrier, a senior lecturer of system dynamics at MIT, “what you really want out of the whole IIoT is the ability to adapt quickly to changes in the environment — not to get everything down to bare bones, but the ability to react and adapt to problems in the environment.”
Despite whatever reservations you may have about adopting IIoT technologies, one thing is clear: no one wants to be left behind while their competitors reap the benefits!
Click the link below to learn more details about how companies are putting IIoT to work and tips for how to be successful with related technologies.
The Industrial Internet of Things: Putting the Hype to Work – Matt LaWell, IndustryWeek
4. What do environmental compliance inspections in China mean for your supply chain?
You might have heard about the rise of anti-pollution inspections spearheaded by the government in China in recent months. Ahead of the Communist Party Congress to be held on October 18th, governmental inspections aim to assess compliance of factories to the national air pollution action plan. Factories in the chemicals, electronics and textiles industries have mainly been targeted, with some temporary shutdowns and even factory closures.
But amid the news stories and rumors surrounding the rise of inspections, you might have found yourself wondering is my supplier and supply chain really at risk? This featured article outlines four steps and questions you should ask to determine the potential of environmental interference in your supply chain:
- Get the list of processes involved in making your product, including the cities where they are carried out.
- Are any chemicals involved in these processes? You’ll need to request a Material Safety Data Sheet (MSDS) for the proper way to handle these chemicals.
- Are any permits required for these processes? Make sure you ask for documentation from your factory for compliance.
- Is the city your factory located in actively driving these manufacturing activities away? Provincial governments typically send out the notifications of inspections to factories, so the scale of inspections might vary based on the city you’re manufacturing in.
Like managing social compliance and product quality, ensuring environmental compliance isn’t as simple as taking your factory’s word for it that they’ve got things under control. This round of environmental inspections might die down after the government’s meeting this month, but attention to environmental issues is not likely to go away soon in China.
So find out more on how to evaluate your factory’s environmental compliance in the article below:
Anti-Pollution Inspections in China: 4 Risks Factors – Renaud Anjoran, China Manufacturing Consultants
5. New worries arising for future supply chains
What comes to mind when you think of supply chain risks facing your business? Do you first think of issues stemming from your individual suppliers, like operational capabilities, the risk of bankruptcy or material and component availability? Or are you more concerned about risks resulting from your sourcing country, like strikes or political instability?
The good news about risks stemming from your supplier is they can often be controlled by better planning and cooperation with your supplier. But a recent study conducted by SCM World shows that supply chain professionals are increasingly concerned about three less controllable risks, namely:
- War, terrorism or other geopolitical issues
- Natural disasters affecting supplier facilities (e.g. earthquakes, floods, etc.)
- Data security/IT incidents (e.g. cyber-attacks)
The percent of respondents who said they were “very concerned” about these risks jumped by 4 percent, 8 percent and 14 percent respectively from 2016 levels. And for data security, now almost half of respondents, or 44 percent, say data security is a serious concern for their business.
There’s certainly not much you can do individually to stop the rise of terrorist attacks or prevent Mother Nature from taking a swing at your sourcing locations. But that doesn’t mean your only option is to throw in the towel and hope for the best. Preparing contingency plans can go a long way in ensuring your business can weather any storm, natural or otherwise, that comes your way. Particularly when it comes to data security, many manufacturers are already finding ways to avoid getting hacked (related: Improve IoT Security with These Defense Tactics).
Check out the link below to read more about supply chain risks you might need to prepare for in the future:
Supply Chain Risk 2020: New Worries – Kevin O’Marah, Forbes
We’re constantly scanning the web for top manufacturing stories and news. If you’d like to submit an article for consideration for our weekly Best in Manufacturing, send us a message and let us know.
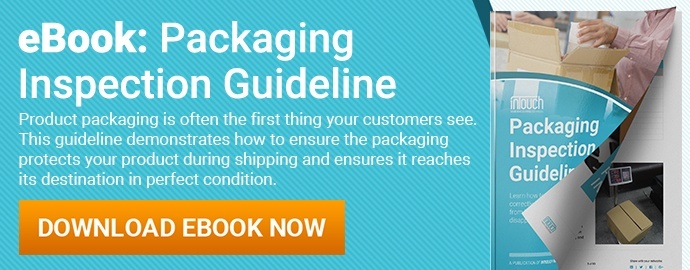