Each Sunday, we publish a list of top articles and other content related to manufacturing in areas like quality control, product development, supply chain management, sourcing, auditing and law.
1. The future of retail, pioneered in China
The U.S. retail sector is increasingly looking like a graveyard. Store closings are everywhere. And major retailers, like Toys R Us, are shutting down completely. It seems like the grim reaper has retailers across the country in his ghastly sights.
But is there hope on the horizon for retailers?
The major Chinese company, Alibaba Group, seems to think so. In the video below, you can get an idea for what the company envisions as the future of retail, dubbed “New Retail”.
Essentially, retail’s future is entwined with smartphones and convenience. Mobile computing will enable shoppers to:
- Scan products to get information about them
- Make purchases
- Schedule home delivery of items
- Compare options
- And more
These advantages aren’t just confined to retailers with their own stores. Alibaba foresees malls and mom & pop stores also benefiting from them and evolving.
Will Alibaba’s model for “New Retail” save battered retailers in the U.S. and across the globe? Let us know in the comments section at the bottom of this page.
To read more about this new retail model, check out the featured article in the link below:
The Future of Retail Is Happening Right Now in China – Alibaba via Quartz.com
2. How much of your product is actually made in China?
The common claim that “everything is made in China” isn’t as true as you might think. The alternative statement, “everything is assembled in China”, would be much more accurate.
According to a recent news article, many of the parts believed to be manufactured in Chinese factories are actually imported from other countries to be assembled into finished goods there. For example, the article cites a 2010 paper from the Asian Development Bank Institute dividing the value different countries contributed to production of iPhones:
- Japan contributed 37 percent by supplying the screen and flash memory
- Germany contributed 17 percent by supplying the camera and power-management circuitry
- South Korea contributed 13 percent by supplying the SDRAM
- China contributed 3.6 percent mostly by supplying labor for assembly
And the iPhone isn’t an exception. Chinese factories still lack the technology needed to manufacture products ranging from robots and semiconductors to ball point pens. Instead, they must import many of the necessary components from Japan, South Korea, Germany, Switzerland, France and elsewhere.
How China’s ambitious plans to further innovation threaten overseas manufacturers
Part of Beijing’s Made in China 2025 plan aims to have Chinese companies domestically producing 70 percent of basic core components and materials used in goods manufactured locally. The problem is China is still very far from reaching that target.
The challenge has given rise to policies that force foreign companies wanting to operate in China to forfeit their proprietary technologies. And Chinese investors have turned to buying foreign companies to acquire the technologies they want.
According to a 2017 paper from the European Union Chamber of Commerce in China (EUCCC) on China’s industrial policy:
In the past, some foreign companies managed to at least partially limit transfers ... and therefore did not compromise their long-term competitiveness. But this has become increasingly difficult.
This news raises questions about the complexity of supply chains and where our products’ components come from. Click the link below to read the full story.
The Lie Behind the ‘Made in China’ Claim - Dinny McMahon, news.com.au
3. Increased labor unrest in China
I wrote about the scale of Chinese labor unrest last year. And since then, labor unrest has only increased. As this featured article reports:
During the first 10 weeks of this year [2018] there were more than 400 publicly reported strikes, more than double the number during the comparable period last year.
More and more workers are demanding their unpaid wages and benefits. But they’re often met with arrests and violence from local police. Such is the life of “troublemakers”.
This featured article reports that strikes are on the rise because of a slowing economy. Herein lies a ripple effect: because of the economy, companies have less money, so they delay or completely forego payments to workers, which leads to strikes. In some cases, a company will close overnight, resulting in disgruntled workers the next morning.
To get an idea of the labor unrest in China, take a look at this map (accurate as of April 4, 2018):
Recorded instances of strikes in China since October 2017, via China Labour Bulletin
To get an up-to-date idea of the scale of labor unrest in China, view this strike map.
Understandably, companies that work with factories that don’t pay their workers adequately or on time are at risk of serious disruptions to their operations. Audits of factories to assess compliance with local laws and respect for employees are one method to prevent supply chain delays before they happen.
To read more about labor unrest in China, check out the full article in the link below:
China’s Communist Party Is Abandoning Workers – Harvey Thomlinson, The New York Times
4. The magic of magnets in product design
Who doesn’t like magnets? To a child, magnets seem like magic–two pieces of metal that push and pull against each other in thin air. To product designers and engineers, magnets can also seem like an amazingly useful, and similarly magical, component for a product.
This featured article lists three main functions for magnets in product design:
- Latching, like a magnetic door or window fastener. The key consideration for magnetic latches is the distance between two parts, as magnetic force decreases as distance increases. The attachment of the magnet to the product, whether with an adhesive or mechanical fastening, also needs to be stronger than the magnetic force itself. Otherwise, the magnet will come detached.
- Interlock, a safety mechanism that signals to a piece of equipment to stop operating when a user accesses part of the device. An interlock is what stops your microwave from running when you open the door. In some extreme environments or sanitary applications, a magnetically triggered sensor can be more effective and easier to clean than a mechanical interlock.
- Attaching, as commonly used in charging cables to attach the cable to your electronic device. Alignment is essential for magnet attachment. Your design will need to align magnets mechanically, as the magnets alone can only provide the holding force. You might also use a series of alternating pole magnets to self-correct misalignment. But this will likely come at a higher price-point.
Magnets are still kind of magical. But trying to fit magnets into your design for a role they’re not suitable for can easily lead to poor product performance.
When working with magnets, it’s essential to develop prototypes and golden samples for your product to ensure magnets perform appropriately. Performing a pre-shipment inspection after production can also help ensure production meets your design and performance standards (related: 4 Ways Importers Conduct Product Inspection [eBook]).
Follow the link below to learn more about the magic, and limitations, of magnets in product design:
Should We Be Drawn to Magnets? – George Turvey, Hardware Massive
5. Made in Hong Kong
“Made in China” is a common phrase you’ll see on products that are sent across the globe. But what about “Made in Hong Kong”?
The author of this featured article interviewed several people from Hong Kong and uncovered some reasons why they prefer Hong Kong for manufacturing over the Chinese mainland:
- Increasing rent and labor costs on the mainland
- A complicated tax system on the mainland
- Worries about intellectual property protection on the mainland
- The free flow of information in Hong Kong
- Designers having a more global view in Hong Kong
But facing Hong Kong are several problems:
- High land costs and constrained space
- Lack of interest from younger generations
- Lack of support from the local government
The article mentions, however, that the Hong Kong Productivity Council (HKPC) has invested over $18 billion in an effort to promote re-industrialization in the region. The government would like this money to contribute to the development of innovative and high-value added manufacturing. Investments like this will potentially help the Hong Kong government reach its goal of manufacturing contributing to 5 percent of GDP.
Are you curious about manufacturing in Hong Kong? If so, check out the featured article in the link below:
Remaking Manufacturing in Hong Kong – Erica Li, Gloria Li and Katie Cheng, HKFP
We’re constantly scanning the web for top manufacturing stories and news. If you’d like to submit an article for consideration for our weekly Best in Manufacturing, send us a message and let us know.
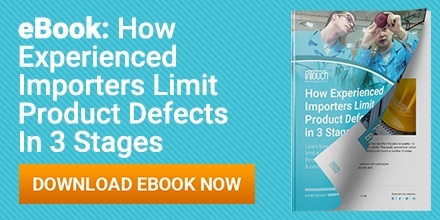