Each Sunday, we publish a list of top articles and other content related to manufacturing in areas like quality control, product development, supply chain management, sourcing, auditing and law.
1. What’s keeping India’s factories from competing with China’s?
The goals for “Make in India” are pretty major. By 2025, the country wants to create around 100 million manufacturing jobs and bring the manufacturing contribution to GDP from 16 percent to 25 percent.
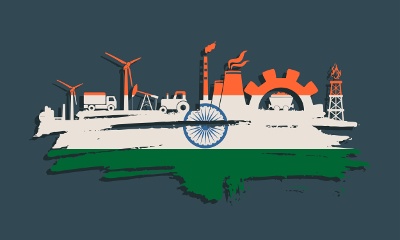
While there’s still 8 years to meet these objectives, it might be slightly harder to boost manufacturing and export growth now that some nations are grappling with protectionist sentiment, like the United Kingdom and the United States.
Aside from trade barrier difficulties, the authors of this featured article mention a few other issues that India must overcome to become a more formidable international manufacturing competitor.
The problems include:
- The number of people in factories: in contrast to countries like the U.S. and Germany where more automation is utilized, in India great volumes of people still perform a majority of the work, which can hamper productivity compared to more automated competitors.
- Quality checks are still performed manually: similar to the point above, automation is limited in typical factories in India, which can sometimes lead to inconsistent inspections. Workers still manually check products.
- Wage competition: India’s service sector is able to provide better wages in some cases than those offered in factories, which makes factories a less competitive employment option. This aspect can affect how long workers stay at factories.
- Lack of training: Indian workers have inadequate knowledge of how to use machines, leading to machine abuse. Machines frequently run until failure instead of having technicians perform preventative maintenance to stop issues from occurring early on.
The article mentions that despite these issues, the labor cost in China, one of India’s top competitors, is almost four times that of India. This cost difference, however, is largely offset by higher productivity in Chinese factories.
Do you think India can overcome these obstacles and become a manufacturing powerhouse? How do you think India’s manufacturing compares to China’s? Let us know in the comments section below.
To read more about Indian manufacturing, check out the full article in the link below:
Role of Productivity, Quality and Jobs in Making ‘Make in India’ a Success – Somshubhro Pal Choudhury and Anil Paranjape
2. Upgrades to Chinese plastic
There are plenty of misconceptions of quality control in China. Despite how Made in China 2025 is helping the country move up the industrial value chain, there are still some people that believe China isn’t cable of producing great products and Chinese suppliers don’t care about upgrading.
But it’s easy to see how some companies are working against those misconceptions when you take a look at several suppliers of plastic making machinery that were around at the recent Canton Fair in Guangzhou.
Present at the Canton Fair were suppliers that are trying to integrate Industry 4.0 connectivity and automation into their products. And on the horizon for some were plans for foreign expansion to better understand and compete with the international market. One company said it wants to open a sales office in California while another said it’s considering opening up a German research center.
Already for some of these suppliers, their machines are used for products eventually sold at major retailers like Walmart and Target. And with more upgrades to their machines in the works, that can only mean better quality and improved customer satisfaction.
If you’d like to learn more about how the Chinese plastic industry is upgrading, check out the full article in the link below:
Canton Fair Shows Chinese Industry Upgrading – Kent Miller, Plastic News
3. China’s efforts to reduce pollution
Pollution in China is sometimes extremely persistent and severe. After my own personal experience of living in Beijing for 8 months, I can safely say that there were stretches of time when the smog simply wouldn’t go away. Or it might, in fact, vanish for a few days, only to come back with a vengeance at higher PM 2.5 levels (the measurement of hazardous particles in the air).
The reality is that the cost of China rapidly industrializing has been damage to the environment. Blue skies, unfortunately, aren’t always the norm in certain parts of China due to heavy industry – like in Tangshan, Hebei province.
This part of China is the focus of this featured article. As the article reports, several significant pollution-causing industries are present in Tangshan, like cement production, steelmaking, chemicals and more. And the province where it’s located, Hebei, is home to 7 of the top 10 most polluted Chinese cities.
In the face of so much pollution, the government has responded in a variety of ways. Mayors of certain areas will sometimes forcibly shut down factories in an effort to meet annual pollution quotas or to clean up the skies in anticipation of a major event. And throughout the country, PM 2.5 particulate recording stations have been established to monitor PM 2.5 levels and better inform citizens. Premier Li Keqiang has also declared a war on air pollution in China.
Certainly, pollution affects manufacturing in China in several ways. And with more government responses to that pollution, factories might shut down in greater numbers to obey the demands of Chinese officials. In some cases, coal factories are also being closed, which while good for the environment, could create power disruptions to factories, thereby hindering production.
Do you think China’s environmental concerns will significantly affect manufacturing? Let us know in the comments section below.
To learn more about China’s response to air pollution, check out the full article in the link below:
China's Surprising Solutions to Clear Killer Air – Beth Gardiner, National Geographic
4. Demand for Asian-manufactured goods swells in Western markets
Two recent events have indicated a rise in more protectionist national policies: Brexit and the election of U.S. President Donald Trump. Yet despite their stance on foreign trade, Asian exports are rebounding in America and Europe thanks to demand from Western shoppers.
According to data from Bloomberg, the 3-month moving average of year-on-year exports has increased since 2016. While exports aren’t quite what they were around halfway through 2008, before the Great Recession, the uptick is certainly appreciated by factories in Asia.
One example the article cites is that of an Indian Garment exporter, Orient Craft. Its founder, Sudhir Dhingra,
…[Dhingra] has seen his exports to the U.S. grow to $181 million in 2016 from $129 million in 2012…
While Sudhir has expressed optimism about this development, President Trump has pledged to review cases of “trade abuse”, which might put many Asian companies like Sudhir’s in danger. And for Asian nations, whose economies are still generally reliant on manufacturing and in some cases agriculture, any barriers to trade might hurt exports and stop the free flow of goods from their countries to the West.
To learn about the rebound of exports from the East to the U.S. and Europe, check out the full article in the link below:
Western Shoppers Are Fueling a Bounce in Made-in-Asia Goods – Enda Curran and Iain Marlow, Bloomberg
5. The fashion industry’s attempts at improving supply chains
The Rana Plaza collapse in Bangladesh in 2013 was a significant moment in social compliance history. 1,135 people died due to a structural failure in the building where countless garment workers worked. After the tragedy, Western brands that had operations in the factories at Rana Plaza received significant international criticism. Walmart and Carrefour are just two out of a number of companies that sourced from Rana Plaza and were targeted for having unethical supply chains.
In the immediate aftermath of the event, this article reports that more than 200 Western brands signed the “Bangladesh Accord on Fire and Building Safety” and the “Alliance for Bangladesh Worker Safety”, in addition to pledging $100 million to enforce them. Despite these good intentions, the initiatives cover only 27 percent of Bangladeshi factories, which leaves many workers vulnerable to an event like the Rana Plaza collapse.
The pertinent question the article mentions is: “how far we’ve [the fashion industry] come since Rana Plaza]”. The conditions found there are emblematic of those found elsewhere, in other developing countries, where worker abuse is “huge”.
Preventing all worker abuse is easier said than done. Even the simplest products can have complex supply chains. A factory that sells jeans, for example, might get buttons from one sub-supplier, fabric from two others and garment labels from another. With so many sub-suppliers, maintaining perfect adherence to environmental and social compliance laws can get tricky. But that’s not always an acceptable excuse for brands and end users.
To win consumer trust in their supply chains, companies like Nike have released a supplier map that details all of their suppliers for the public to see. Yet as these sorts of maps demonstrate, brands can have countless suppliers and sub-suppliers that all need to meet certain standards. And in the words of the CEO of supply chain management firm Segura:
There are weak points throughout the fashion supply chain where negative things can happen and exploitation does occur – in terms of both the environment and the lives of the people that work in the garment industry.
Importers that want to keep these issues out of their supply chain can consider using factory audits to ensure compliance. Otherwise, without at least semi-regular factory checks, workers might suffer and brands might experience the fallout of consumer backlash.
To learn about compliance and the fashion industry’s attempts at improving its supply chains, check out the full article in the link below:
How Fashion Retail Is Cleaning up Its Supply Chains – Timothy Anscombe-bell, Drapers
We’re constantly scanning the web for top manufacturing stories and news. If you’d like to submit an article for consideration for our weekly Best in Manufacturing, send us a message and let us know.
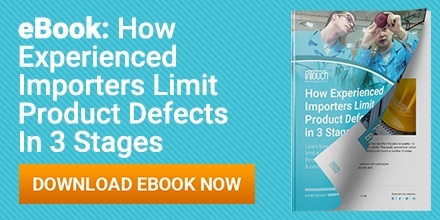