“We already have a QC team”. If you’ve raised the topic of quality control inspection with your Chinese supplier before, you might have heard this response. It’s usually followed by your supplier contact‘s assurance that their QC team will catch any and all quality issues before your order leaves the factory.
Should you believe them?
The short answer is, unfortunately, probably not. When it comes to China quality control, your choice of who will inspect your products can make a world of difference in the quality you receive. And most importers agree that relying on factory QC staff alone just isn’t a reliable solution to managing product quality. Pre-shipment inspection conducted by someone independent of the supplier is the bare-minimum oversight most experienced importers demand (related: 4 Ways Importers Conduct Product Inspection [eBook]).
Read along for the basics of how to get started with pre-shipment inspection and what you need to do as an importer for effective China quality control.
Why isn’t factory QC enough for quality control inspection?
A Chinese factory’s QC team usually consists of internal factory staff designated for quality control tasks, not external inspectors. This doesn’t mean this layer of quality control is unnecessary. Factories can and should have staff dedicated to checking their products regardless of the customer’s inspection requirements.
The factory’s own QC checks might suffice for lower-cost products with looser quality standards, like promotional goods. Promotional goods typically aren’t meant to last a long time. And end-users of promotional goods generally don’t expect high quality because they pay little or nothing for those products.
But importers that purchase other types of products from Chinese suppliers often won’t accept the risk of product quality issues going overlooked by factory staff. Instead, they typically insist on arranging inspection with another party before shipment to avoid a few common problems.
Cultural barriers contribute to misunderstandings
Misunderstandings caused by cultural barriers are a common problem when relying on Chinese suppliers to meet expectations. For example, you might encounter a lot of “yes men” at Chinese factories, contacts that rarely say no to a request or object to your opinions.
You might not recognize a problem in your communications at first. Your supplier is cooperating and able to carry out all of your requests, right? But this behavior might be rooted in a cultural misunderstanding that can come back to hurt your business later. In Chinese business culture, workers are traditionally expected to follow rules and instructions without raising questions or speaking up with suggestions or direct feedback.
Confusion often results, leading to unpredictable delays, product quality issues with your order and unmet expectations. Perhaps the factory owner knows they’ve already hit order capacity and cannot feasibly meet your production timeline. But instead of telling you upfront, they rush the order to meet the deadline or ignore the deadline altogether.
Other times Chinese factory staff may hesitate to ask important questions about your product requirements for fear of looking inexperienced or unprofessional. Then there’s a good chance you’ll find serious nonconformities and other product issues when you receive the shipment later (related: Why You Can’t Assume Chinese Suppliers Always Understand Requirements).
Awareness plays an important role in any type of cross-cultural activity. Manufacturing is no exception. At the very least, you should always try to anticipate potential problems by:
- Providing clear requirements for your products
- Asking your supplier direct questions; and
- Taking a proactive approach to quality management by insisting on pre-shipment inspection
Don’t expect your supplier to take the initiative and notify you right away when any issues arise.
Conflicts of interest and minimal reporting of product QC issues
Another common problem with having factory staff inspect your products is there’s an inherent conflict of interests. Your greatest priority is probably getting your product manufactured to meet a price and quality standard your customers will be happy with. Whereas the factory owner and their staff tend to be most concerned with manufacturing your product as cheaply and quickly as possible.
Addressing quality issues requires both time and money, which conflicts with a supplier’s desire to process and ship out orders as quickly as possible. This means the factory’s QC staff may not send you an accurate report of the status and condition of your order, if they send you one at all. And you’re not likely to see test results, photos, descriptions of the types of quality issues they find or other details.
Factory QC staff that lack adequate training or testing equipment
It’s not uncommon for factory QC staff to lack adequate training to use important product testing equipment. For example, inspectors often use a color matching light box when checking fabric to confirm color requirements. But though a factory representative might send you a photo of the light box their QC staff used to test the fabric, those staff may not be trained to use the equipment properly. Or worse, the factory may not actually have the equipment on site and workers haven’t run the testing at all.
It’s possible to manage your product QC with only factory staff checking your goods. But it usually takes a deep understanding of the processes required in manufacturing your product, cultural barriers and all potential quality issues that could arise. This usually only comes with years of experience working with the same supplier, who you know you can trust and reliably communicate with.
Better China quality control inspection options for first-time importers
A pre-shipment inspection can catch a lot of “easy” issues before the goods are shipped to your home country, where reworking your goods would be more expensive and difficult. Some issues importers commonly face include:
- Product or packaging color doesn’t match samples
- Carton markings don’t match requirements
- Item dimensions don’t match samples or are out of tolerance
- Dirt, dust or excess glue on a product
- Scratches, holes, chips or other damage to the product
You’d probably like to avoid these issues if possible. But if you can’t always rely on your factory to catch quality issues, what are your options for China quality control?
Travel to China to personally conduct product QC
So if factory staff don’t reliably put your interests first or understand your product requirements, who will? The obvious answer might be yourself or your own business personnel. You can consider coming to China yourself to check the finished goods or send someone from your company on your behalf.
After all, who better to inspect a product than the customer that sets the quality standard? And you might want to visit your supplier’s factory anyway if you’re considering a long-term relationship. But keep in mind that knowing your product doesn’t necessarily mean knowing the best way to conduct an inspection (related: Why Most Importers Don’t Conduct Product Inspection Themselves).
If you want to effectively inspect on your own, you’ll need to consider many details about the process and perhaps even receive training before inspection. Professional QC inspectors follow industry-standard procedures for sampling and on-site checks and tests that give statistical validity to inspection results. For example, some of the inspection details you’ll need to decide prior to traveling to the factory include:
- Inspection quantity - Will you inspect 100 percent of your order or a sample size? How large of a sample size will you inspect to reach a reasonable pass or fail result?
- On-site testing - What on-site tests will you conduct on the product? What’s the required testing procedure? How much time will you need for each test?
- Tools / equipment - Do you need any equipment to check your product? Will the factory provide this or do you need to bring it to the factory yourself?
Traveling internationally to China to conduct inspection yourself is doable if you prepare ahead of time and don’t require regular or frequent inspections. But if you have regular shipments from China every month and need inspection, this likely won’t be the most cost-efficient option. Considering your travel costs, time and the opportunity cost of neglecting other business activities at home, you might prefer to hire an experienced professional to inspect for you.
Hire your own full-time inspectors to conduct product QC
To meet the needs of regular inspections, you might consider building your own QC team in China. Hiring your own full-time inspection staff has a number of benefits. Full-time inspectors can often:
- Directly communicate with you on your own terms
- Make decisions right away on whether or not to ship orders based on inspection results
- Be employed under your company, accountable to your company culture and contractual obligations
- Be more cost-effective when inspections are needed often
But legally hiring inspection staff in China often involves setting up your own office in China, which comes with its own challenges. You’ll need to understand how to comply with applicable labor laws to:
- Legally set up your office – this includes setting up a China compliance program to protect against potential anti-corruption problems, meeting minimum capital requirements and overcoming several other challenges
- Legally hire staff – which means meeting particular tax and salary requirements and navigating China’s complex labor laws
- Legally terminate an employee when necessary – which usually requires a severance payment and proof that you fired the employee based on statutory grounds
Another important consideration with hiring full-time, salaried inspectors locally is the cost advantage diminishes when during idle periods. Unless you need inspections regularly and often, it can be very expensive to pay and maintain full-time staff.
Most new importers don’t have the order volume to justify hiring full-time staff. But if you do choose this option for inspections, it’s a good idea to seek professional legal counsel to ensure compliance to all applicable laws in both your home country and in China.
Hire a third-party inspection company to conduct product QC
Many importers, both new and experienced, choose to hire a third-party inspection company on an as-needed basis. This may be a good option for you if you’d like to pay greater attention to product QC, but don’t have a big budget to fly to China or hire your own staff. Hiring a third party might sound like a big commitment, since you’ll need to pay upfront for inspections.
Detailed, unbiased reporting of quality issues
You can generally expect a similar depth of reporting with most professional third-party companies that you might find when hiring full-time inspectors. Inspectors will typically issue your report with a “pass”, “fail” or “pending” result depending on the number and severity of any quality issues they find (related: What QC Inspection Results Do and Don’t Mean for Your Shipment). Your inspection report should include all of the following:
- Total quantity of finished and packed units found at the factory, to ensure accurate order quantity and adherence to your production timeline
- Number and type of defects found in inspected units
- Any nonconformance with provided specifications
- Results of any on-site testing for performance, functionality and safety
- Photos of inspected units, packaging, test results and any defects or other findings
And like full-time inspectors, third-party staff tend to represent your interests when visiting the factory. These inspectors should have no relationship with factories outside of inspecting their client’s products. They shouldn’t refer clients to particular suppliers and should never have personal relationships with factory staff, which can often lead to integrity problems. This independence from the factory ensures that inspection results remain independent and unbiased.
No long-term commitment for ongoing inspections
Unlike hiring full-time staff, working with a third-party QC provider typically doesn’t require a long-term commitment. You don’t need to set up a local office and understand China’s employment laws. You also don’t need to meet a minimum order volume or value for inspection, nor do you need to pay for multiple inspections upfront.
You can pick and choose when you’d like to conduct inspection at your leisure, according to your business needs. Third-party inspections are usually charged by man-days, or time spent at the factory. So you don’t have to worry about paying for time you’re not using. And most product inspection companies will work with you to meet your budget, such as by quoting a one-man-day option.
What’s the importer’s job in managing China quality control?
Working with a third-party inspection company can save you a lot of effort and time. But it’s not a “hands-off” process where you can just request the inspection and wait for your order to arrive. You’ll still need to do your part to ensure inspections run smoothly.
As an importer, you’ll still be responsible for:
- Clearly communicating your product and inspection requirements to the supplier (well before mass production) and to inspectors (well before inspection)
- Introducing outside inspectors to your supplier and arranging inspections
- Reviewing your inspection report for any issues
- Notifying your supplier of any corrective action you expect them to take before shipping
- Updating your product specifications for future orders with any new issues your supplier and inspectors should know of
Remember that inspection companies don’t have any leverage over the supplier to make factory staff listen to or follow their instructions. Third-party inspection companies cannot compel your factory to follow through with corrective action or other changes. Ultimately, only you have leverage over your supplier because you’re paying for the order. You, as the importer, must arrange for next steps and push your suppliers towards the appropriate action directly.
Considering your China quality control inspection needs
Quality control inspection works best when the importer has a clear understanding of their product requirements and inspection needs. Before choosing a quality control inspection method, you might consider a number of criteria, including, but not limited to:
- The history of quality issues for the item and with the factory
- The value of the item, your target market and customers
- Product requirements and potential quality issues
- Production and shipping deadlines, to ensure you have enough time to schedule a final inspection
- Your customer or distributor’s requirements for inspection (e.g. some retailers require a third-party to inspect products before shipping)
Providing the necessary information in a QC checklist to your factory and inspection company can help keep all parties informed of your requirements (related: 5 Essentials of a QC Checklist [eBook]).
Conclusion
You’ve probably already invested a lot of your own personal time and money in getting your importing business off the ground. You’ve already gone through the hard part of developing a business plan, analyzing the market and choosing a product and a supplier. You’re almost to the finish line. But don’t let product QC be your downfall.
When it comes to any new venture, mistakes are inevitable. That’s part of the learning process after all. But taking shortcuts on product QC, like relying on factory staff for inspection, can sabotage all your hard work in the blink of an eye. Pre-shipment inspections by someone outside the factory will help you delight your customers with better products and take your business to greater heights.
Have any advice for new importers regarding China quality control? Share your best practices in the comment section below!
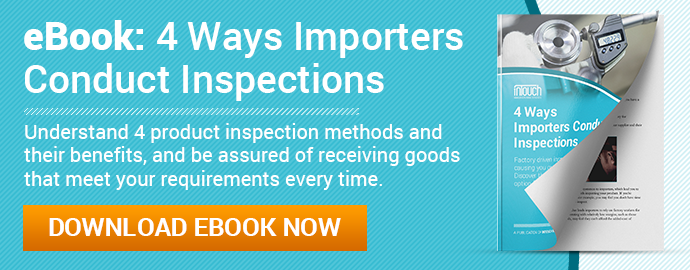