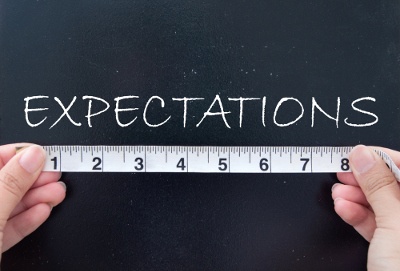
Have you ever had to adjust the quality standard applied to a product you’re manufacturing abroad?
Maybe you, like most people, don’t like change. But manufacturing and sourcing are dynamic industries. And few successful importers and retailers can neglect adapting to changing suppliers, regulations or customer expectations and remain profitable in the long run.
When you’re relying on acceptable quality limits, a.k.a. acceptable quality levels (AQL), as your standard of quality for consumer products it’s sometimes necessary to adjust your AQL. As the minimum quality level a shipment is required to meet for you to accept it, AQL should change with quality expectations for your products (related: The Importer’s Guide to Managing Product Quality with AQL [eBook]).
But many importers start using one AQL standard and stick to it for subsequent production runs and QC inspections without much forethought. Like them, you might be neglecting a valuable tool that can make your inspection results and your products better reflect your and your customers’ quality expectations.
What are the most commonly used acceptable quality levels for pre-shipment inspection?
There’s no set AQL standard importers should apply when manufacturing and inspecting any particular product. Each importer often has unique quality expectations and standards. So no quality expert can tell you exactly what AQL you should set for your goods.
But there are some generally accepted guidelines among different product types that offer a good starting point for importers. Many importers start with these AQLs when first conducting a pre-shipment inspection. And they’re what third-party QC providers often use when inspecting on behalf of importers that have no established guidelines of their own.
Importers usually set a different AQL for each type of defect, namely “critical”, “major” and “minor” defects (related: 3 Types of Quality Defects in Different Products). This is because importers usually have a different tolerance for different kinds of defects.
Not all defects pose the same level of risk to your brand and consumers. You’re probably more likely to accept a large portion of an order with subtle, aesthetic imperfections (minor defects) than one with defects that pose serious safety or liability risks (critical defects).
Importers often apply a stricter AQL standard for E&E products than for general softline or hardline consumer products because major defects in E&E products can often cause serious functionality issues. Manufacturers in the aerospace, automobile, industrial or medical device fields often apply an even stricter standard, or even a zero acceptance plan.
Due to the severity of critical defects, almost all importers, regardless of product type and brand, agree that the AQL for critical defects should always be zero or near zero.
But you can, and should, tighten or loosen your chosen AQL for major and minor defects if the above industry standards don’t meet your needs. Two importers of similar product types may use vastly different AQLs. You might adjust your AQL depending on your:
- Supplier relationship
- Customer expectations
- Product price point
- Target market’s regulations
Let’s take a look at how each of these factors might influence what AQL standard you choose for your next order.
Adjusting your AQL based on your supplier relationship and history
Most suppliers in Asia should be familiar with AQL, as it’s one of the most common single-sampling systems for pre-shipment inspection and reporting among importers. But it’s still up to you as an importer to set appropriate standards based on your relationship with your particular supplier.
Ask yourself a few relevant questions about this relationship when deciding AQL:
- Have you worked with this supplier before?
- Have you found serious quality issues in previous orders with this supplier?
- Can your supplier reasonably meet your quality expectations?
Answers to these questions should offer clues into how strict or lenient your standard should be. Let’s look at how your supplier relationship might determine when to adjust your AQL.
Changing your quality standard when working with new suppliers or new products
Imagine you’re working with a new supplier to manufacture a new product. Your anticipation grows as your launch date approaches. Dozens of hopeful customers pre-order your product.
Then, just before the first shipment leaves the factory, you’re hit with crippling anxiety when you discover your supplier applied the wrong quality standard. Your goods have problems. And your product launch will be a flop marked by returns and negative customer reviews.
How can you prevent this kind of QC nightmare?
Carefully consider your AQL when working with a new supplier or launching a new product. There’s always some uncertainty when facing either of these changes. That’s why importers sometimes start with a small trial order before placing a larger one. And you might start with a relatively strict or lenient quality standard. But be prepared to adjust AQL, depending on the results of the first order.
What about AQLs for suppliers you’ve worked with before?
It’s often easier to set AQL standards for a supplier you’ve already worked with because you have a history of results to help determine appropriate quality expectations.
You might need to tighten the AQL standard if the number of defects found in earlier shipments you accepted doesn’t match your expectations.
For example, you might initially apply an AQL of 6.5 for minor defects to an order of 400 tablet PCs you’re importing. This corresponds to an acceptance point of 7 minor defects for a sample of 50 units, per your AQL table. Then multiple QC inspections have all found 6 or 7 minor defects in the sample, which you decide is actually too many. You could raise your standard, tolerating only 5 or fewer minor defects in the future, by changing your AQL for minor defects to 4.0.
Does setting an AQL standard give your supplier an excuse to manufacture poor quality products?
Some importers worry that AQL sampling gives their suppliers license to produce defective products. And in a sense, they’re right.
Mass manufacturing almost always results in some quality issues, no matter how minor. And to expect perfect production runs with units that are defect-free and identical from one to the next is unreasonable for most importers. That’s why many quality professionals have gradually adopted acceptable quality limits in place of the original term, acceptable quality levels.
Still, applying an acceptance sampling standard like AQL to production and inspection can help you and your supplier reach an agreement on what’s expected. And without a clear way to quantify and relay quality expectations, you’re far more likely to be surprised (often unpleasantly) when you receive your finished goods.
Discuss with your supplier before production to ensure product quality expectations are achievable
It’s essential to clearly communicate your expected AQL standard to your supplier before production. Include your requirement in your purchase order so this standard is clear upfront (related: Prevent Quality Defects in Your Products by Clarifying Requirements). This helps hold your supplier accountable in case there’s any disagreement later.
Discussing AQLs with your supplier beforehand also ensures your supplier can actually meet your requirements. There may be multiple limitations that might explain why your quality expectations are unreasonable for a particular supplier, such as:
- Equipment and technology available: your supplier may lack certain equipment needed for greater precision or more consistent product quality
- Skill level of workers, especially for labor-intensive production processes
- Expected price for order: if you demand an excessively low price for the goods, your supplier may be forced to use lower-quality components or materials
- Order volume and deadlines: tight deadlines and high order volumes can lead to rushing production, worker carelessness and quality problems
Properly negotiating with your suppliers and conducting a factory audit before placing an order can help you avoid the above issues that can cause quality problems. But if your supplier still can’t produce to meet the standard agreed upon upfront, you may be better off finding a new supplier that can.
Adjusting your AQL based on your target market and customers
Your supplier isn’t the only factor you need to consider when adjusting your quality standard.
Say there are two U.S.-based importers sourcing ballpoint pens from the same factory in China. Would both choose the same AQL standard for their products just because they’re sourcing a similar product from the same factory?
Not necessarily. These two importers and their intended customers may have very different quality expectations. Let’s assume “Importer A” is sourcing a one-off shipment of pens for a promotional event. While “Importer B” is a self-funded startup company promising to give its customers a unique and refreshing writing experience. How would you expect their AQL levels to differ now?
There are multiple angles to consider before making a decision that will affect the quality of your product. Your selling price, customers and applicable regulations in your intended market should all have a direct effect on the acceptable quality limits you hold your supplier to meeting.
Product price point and AQL
Customers generally expect a higher quality tolerance for products with a lower price point and a lower quality tolerance for those with a higher price point.
If Importer A above performs inspection before shipping, we can expect the AQL standard used would be relatively lax. The importer’s main concern is that the pens function and there’s no serious issue with branding or product safety. The product is not meant to last a long time and customers will receive it free. So the importer would be far less concerned with the durability of the pens or any scratches or other light aesthetic imperfections.
Meanwhile, Importer B would likely use a much stricter AQL and include many more inspection criteria for their inspection. The same factory would be subjected to a more rigorous set of tests and standards. And this importer would probably be concerned with durability, look and feel, as well as safety, function and branding because their customers are paying for the pen.
How customer expectations inform AQL standards
Customer expectations are typically closely related to the intended price point for a product. And customers will have higher expectations for a higher-priced good or luxury item. But you might find your customers have a higher tolerance for certain defects than you initially thought.
For example, your customers may not mind receiving products with more minor defects, like a few untrimmed threads on a garment, than your current AQL standard allows. Loosening your AQL standard can save you time and money that might otherwise be needed to re-inspect shipments that narrowly failed earlier inspection (related: How AQL Sampling Affects Your Product Inspection Results).
But be cautious when loosening AQLs, as you might find your customer’s standards are higher than you think. Or you might face unexpected quality issues with your supplier that you didn’t experience before.
It’s far more common for importers to need to tighten their AQL standard to address high product returns and complaints they’re receiving around certain quality issues. Tightening your product quality standard can help you meet higher customer expectations. But doing so abruptly may also adversely affect your relationship with your suppliers and raise your costs.
Legal requirements governing AQL for your product type
For certain heavily-regulated industries, shipments must often meet mandated quality standards and AQL standards. Legal requirements are more common for products that can pose a safety hazard to consumers if defective, like those in the medical industry. For example, the U.S. Food and Drug Administration’s (FDA) Code of Federal Regulations requires surgeon’s gloves to meet a 1.5 AQL standard, while patient examination gloves must be inspected to meet a 2.5 AQL standard.
It’s always important to check for legal requirements in each of your intended markets, as they often vary across locations. For instance, while the FDA imposes a 2.5-AQL standard on patient examination gloves, the European Union enforces their own stricter 1.5-AQL industry standard.
Aligning AQL standards with your customers’ and retailers’ expectations
You may face a number of issues if your quality expectations don’t align with your customers’ and retailers’ expectations, including:
- High product returns and customer complaints if your chosen AQL is too lax
- Refused shipments at retailer’s warehouse, if you’re working with retailers that impose their own standards on their suppliers
- Delayed shipments if orders repeatedly fail inspection due to an excessively strict AQL standard, potentially requiring rework, re-inspection and longer lead times
Quality issues related to AQL standards that are too lax often cause more problems for your brand than standards that are too strict.
But you might find your customers or retails are actually more concerned about delivery timeliness than certain quality issues in the shipment. You might loosen your quality standards slightly to allow shipments to leave the factory faster and cut down on costly rework time.
Conclusion
Quality expectations rarely remain unchanged for an importer. The longer you manufacture, the more customers you sell to and the more suppliers you work with, the greater your chances will be of needing to re-calibrate your standards at one time or other.
A tighter AQL won’t necessarily be more beneficial to you and your products, if it doesn’t reflect what your customers want or what your supplier can actually meet. Instead, the key is to ensure the chosen product quality standard matches your and your customers’ expectations and is achievable by your supplier.
Managing quality standards should never be a “one-and-done” endeavor. Always be on the lookout for opportunities to adjust your AQLs and inspection criteria to better meet customer expectations.
Have has the AQL standard governing your manufacturing changed over time? Share your experiences in the comment section below!
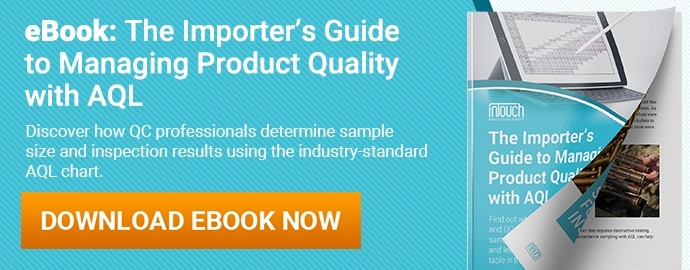