Imagine that you manufacture raw textiles at a factory in China, and you’re concerned about product quality. After considering your options for product inspection, you decide to hire a third-party QC company to check the rolls of finished fabric before the factory ships them. The fabric ends up failing inspection when the QC team reports a high number of oil stains on the product and mislabeled packaging.
What can you do to remedy these issues? If you’re like some importers, you may think it’s your inspectors’ duty to work closely with factory staff to find and fix these problems at the source. But generally this isn’t the case. In fact, this belief that a QC inspector’s role extends beyond simply finding and reporting problems is one of five misconceptions of QC inspection in China.
The reality is that inspectors rarely work with Chinese factory staff to fix issues. So what’s stopping them? And why do importers continue to rely on QC inspection to manage the quality of their products, despite this limitation? Let’s jump into why QC inspectors don’t typically offer remedies to quality control problems and discover how they really benefit importers.
Why QC inspection doesn’t directly solve your quality problems
Product inspection isn’t a magic wand that can cast away all your China manufacturing woes. You can’t offload all your manufacturing concerns to a QC company and expect them to solve all of the problems at your supplier’s factory. Professional QC inspectors are limited in both their authority and scope of knowledge. Whether you’ve a hired a third-party, full-time staff or you’re traveling from abroad to conduct inspection yourself, inspection has its limitations.
Product inspectors aren’t qualified in root cause analysis
Sometimes QC inspection reveals simple, straightforward problems with a product. Let’s say that inspection finds that packaged goods stacked near the top of a pallet are crushing those cartons near the bottom of the pallet. Clearly, the factory must change part of their packaging process, perhaps by providing more protective material inside the carton. But your typical QC inspector isn’t a packaging engineer. And they usually lack the expertise needed to pinpoint the exact problem and advise the best solution.
Likewise, if you’re manufacturing jewelry in Yiwu, Zhejiang Province, your inspector may report that the silver components on the product have oxidized. But that inspector probably isn’t able to say what processes are responsible for the tarnished silver. Such insight may require controlled laboratory testing to confirm material composition or a process audit to identify the root cause. Both of these are outside the capabilities of a typical product inspector.
Even if the average inspector was able to find the root cause for problems and advise the solution, the affordability of services might change because more is being provided. Inspection services might become out of reach for some importers when all they really want is a basic pre-shipment check of their order. By limiting the scope of inspections to checking and reporting, the inspection process is more efficient, requires less time to complete and saves you money.
Product inspectors can’t tell factory staff what to do
Working with a factory to actually address any problems found during inspection requires cooperation from factory management and staff. And corrective action, such as product rework or replacement, usually comes at a cost to the factory owner. The factory often needs to use more product parts & materials, as well as occupying production equipment and workers in the process. Depending on how valued you are as a customer, it can be difficult to get your Chinese supplier to comply.
But it’s typically much less likely that your supplier will comply with a similar request from outside inspection staff. Third-party and other outside inspectors have no real authority to dictate how a factory operates. These staff are often limited to only visiting certain areas in a factory and reporting on certain aspects of production (related: Why Product Inspection Companies Can't Compel Your Chinese Suppliers). It’s also common for factory staff to prohibit certain on-site tests you may have asked your inspectors to perform.
A factory’s own internal QC inspectors can and sometimes do dictate changes on the production line. They’re normally separate from ordinary line workers and report to a manager that has the authority to halt production. But most importers don’t rely on these staff for inspection, due to a usual lack of transparency and the risk of biased and unreliable reporting to the importer.
How QC inspection actually helps you solve quality problems
It’s clear that inspectors are limited in their ability to find causes for and fix product issues they discover in a factory. But the real value they provide to importers can be summarized in one word: transparency. Inspectors provide transparency in their communication, their documentation and their reporting. In each case, they help the importer understand what’s really happening with their Chinese supplier, empowering the importer to make informed decisions about their products.
The inspectors’ role in improving communication
Importers often report difficulty communicating with their Chinese suppliers. They may find that their supplier misunderstands their product requirements. Other importers are misled by a supplier contact that seems to only tell them what they think their customer wants to hear, such as advising an earlier delivery date than what’s realistic. And then there are importers that meet problems simply because their Chinese supplier withheld important information or neglected to ask the importer to clarify expectations.
Staff of inspection companies are often locally-based and have experience moderating the relationship between Chinese suppliers and foreign buyers. And whether the result of a language barrier or a cultural difference, inspectors can often help you avoid misunderstandings and improve communication.
Not only can your inspector communicate with staff at the factory during inspection, they can also help clarify your requirements when liaising with the supplier to schedule inspection. The result is more clarity and a lower chance of nonconformities and quality defects in your finished goods.
Inspectors and QC checklist development
Even experienced importers sometimes don’t know how to effectively clarify their expectations to their Chinese supplier. The best way to do so is typically to combine all of your requirements for product, packaging and inspection method into one document called a QC checklist. And QC inspectors can be a great help to you in collaborating on the criteria used for assessing your product.
Professional inspectors often have experience checking products similar to yours and can advise specific on-site tests and other standards that are relevant to your product. For example, let’s say you’re manufacturing stainless steel kitchen knives in a Chinese factory. You may want to have a testing procedure in place to check blade strength during inspection. And an inspection team with relevant experience can recommend an efficient and accurate standard for this.
This collaboration on inspection criteria helps you ensure that any quality defects or nonconformities are caught before the product ships.
Checking your product and reporting on any issues
The main role of a QC inspector is to identify and report issues based on the standards agreed upon by the customer and supplier. For instance, China product inspection providers thoroughly check goods via visual inspection, perform on-site tests, confirm packaging durability and conformance to standards and more. The inspector generally carries out a service in the following steps:
- Factory management picks a date it can accommodate an inspection and invites the inspector to perform the service then.
- Inspection staff visit the factory and check the product according to the customer or importer’s criteria.
- Any issues found are documented on-site in a detailed report, which is then sent to the importer for review.
Based on the findings shown in the report, the importer makes a decision whether to ship the order. As the importer, you might request a re-inspection based on different standards, ask the factory to take some corrective action or choose to accept the order despite any issues reported. In some cases, you may even want to ask the factory to destroy defective units while a third-party supervises.
Whatever you decide, it’s generally up to you to address any problems directly with your supplier. The inspection report and the result shown merely help you make an informed decision, giving you transparency to see the true status and condition of your shipment.
Conclusion
Acting as your eyes and ears on the ground is what QC inspectors excel at. They give you a snapshot of order quality and status. But a third-party doesn’t have the same relationship you have with your supplier. If your goal is to fix issues with an order or factory, you need to be the one to directly address these with your supplier and jointly determine what action is needed next.
You know the kind of product you and your customers expect. And Chinese suppliers are more likely to take action to fulfill a request of their customer than of some outside third-party. Ultimately, successfully addressing product QC and nonconformities requires cooperation from both the supplier and the importer. A QC inspector can only reveal to you important information you might otherwise not see.
How has pre-shipment inspection helped you solve problems working with a Chinese supplier? Share you experience in the comments below!
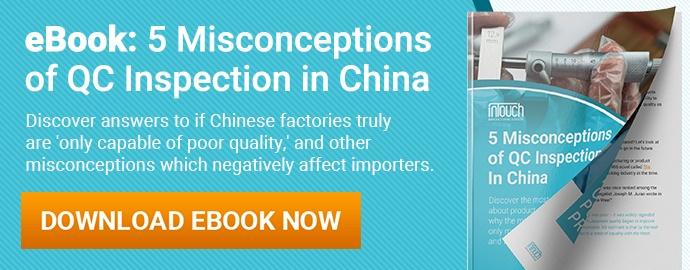