Imagine spotting a jacket you really like through the window of a store. You didn’t leave home today wanting to buy a jacket, but something about this particular one struck you immediately. You head into the store, find the jacket and try it on, feeling the cool, silk inner lining slide along your arms. But when you go to zip the jacket up, the fabric gets caught in the zipper.
Would you buy it?
Many consumers wouldn’t. Others might buy it, encounter the problem later and then return the jacket for a refund.
It’s a shame so many garment importers overlook issues like a broken button or zipper when these can easily be caught during an inspection and fixed at the factory before shipment. Why would you ever risk your customers finding these issues with your product when shopping?
Checking accessories is a vital part of any effective garment inspection (related: Garment Inspection Guideline [eBook]). Since function and durability are essential to the quality of garment accessories, on-site testing, in addition to visual inspection, can be particularly helpful for evaluating garment accessories.
Let’s look at five examples and how to specify each in your quality control checklist.
Including on-site testing procedures and sample sizes in your garment inspection checklist
Clarifying requirements for on-site tests and checks with your supplier and your inspectors before inspection helps prevent confusion. Many importers choose to combine their requirements in a central document called a QC checklist. When it comes to on-site testing for garments, your QC checklist should typically specify:
- The testing procedure for each on-site test required
- Your desired sample size for on-site tests, whether a fixed number of pieces or a special or general inspection level sample size using AQL sampling
- Equipment required for each specific test and who should provide it, namely the importer, the factory or the inspector
Inspectors can often only carry handheld tools like a barcode scanner, calipers and a tape measure with them to a factory. Don’t assume that any other equipment your inspectors need for checking garments will be available at the factory. Instead, tell your supplier in advance if there’s equipment the factory must prepare.
Garment QC professionals normally don’t recommend performing on-site testing for every single piece in a clothing inspection sample size. Sample sizes can range up to hundreds or even thousands of units. So conducting tests on the full sample size can be very time consuming, and ultimately, lead to higher inspection costs for importers.
Besides being expensive, testing every accessory is often unnecessary because there tends to be less variance in the processes and materials used during mass production. So for many (but not all) tests, garment QC professionals recommend conducting on-site tests on either a fixed number of pieces or an AQL special inspection level.
Let’s take a look at five of the most common on-site tests and checks for garment accessories and how to include each of these requirements in your QC checklist.
1. Pull test to check strength and security of garment accessories
Accessories are parts added to the garment, usually by stitching. Testing the strength of the stitching or other bonding material is a necessary step in most garment inspections. And a simple pull test is one of the most common ways to test.
To conduct this test, an inspector often uses a handheld pull gauge, or tabletop pull test machine, to apply a specified force to the accessory for a certain amount of time. If the accessory detaches from the garment, the result of the test will be “fail”.
Third-party inspectors generally use international standards to determine the level of force to apply to the accessory. Your standard might differ depending on the type of accessory you’re testing. And certain government agencies, such as the U.S. Consumer Product Safety Commission (CPSC), place greater emphasis on securing accessories to infant and children’s clothing, especially buttons and others that could cause choking.
How to specify a pull test requirement in your QC checklist
A pull gauge or pulling test machine is a tool garment factories commonly have on site. But inspectors might not always have access to it for every inspection. Maybe on the day of inspection an internal factory QC employee needs to use the equipment. Or it might have recently broken and the factory hasn’t replaced it yet.
If a working pull gauge isn’t available at the factory, it’s common practice for the inspector to simply conduct the pull test by hand and note this change to procedure in their report. Testing by hand won’t be as accurate as the result from a pull gauge. But if an experienced garment inspector can easily remove the accessories by hand alone, testing by hand can still reveal an issue the factory needs to address.
Include all of these instructions in your checklist, including what to do if there’s no relevant equipment on site. Importers often omit this kind of contingency plan and then have to repeat inspection because they need the testing result before approving the shipment.
2. Fatigue test to check the durability and function of garment accessories
Inspections for many product types include testing longevity by using the product as intended for a number of cycles. Garments are no different. Importers often request a fatigue test to verify the function and durability of accessories during clothing inspection.
Take hook and loop fasteners, or Velcro, for example. A children’s pant with a Velcro closure would be pretty useless if the two pieces of Velcro didn’t stick together and come apart with reasonable force. You might check by pressing the two corresponding pieces of Velcro together and then pulling them apart.
An inspector would repeat this process a certain number of times, following ASTM D5170 or a similar standard, as part of a fatigue test. They might even use a peel test machine or Velcro fatigue tester for more precise or prolonged testing:
Other fatigue tests might include zipping and unzipping, buttoning and unbuttoning or snapping and unsnapping a garment. Garment inspectors will usually perform the test for 50 cycles and check for any loss of function throughout the test.
How to include a fatigue test requirement in your QC checklist
Like the pull test, inspectors usually conduct the fatigue test on just two pieces per style, instead of on a larger sample size. If you have multiple types of accessories on your garment, be sure to clarify whether your standards or procedures for on-site testing vary for each kind of accessory.
A more intensive version of the fatigue test can be performed in a lab environment with specialized equipment. But unlike the pull test, inspectors more often perform the fatigue test by hand during a regular pre-shipment inspection. This is usually sufficient to simulate regular customer use and reveal any defective accessories.
3. Stretch test for elastic fabric and straps
If you’ve ever owned a pair of pants with an elastic waistband, you’ve probably noticed the elastic wears out over time. Faulty elastic can make the garment unwearable when it’s meant to hold the garment in place and allow it to stretch in size when worn.
Some loss of function may be inevitable over the lifetime of the product. But ensuring any elastic garments leave the factory in new condition is a top priority for most garment importers.
A stretch test is intended to check the stretch, elongation and recovery of elastic fabric or accessories, such as straps or ties, on a garment. During the test, the inspector stretches the elastic by hand and checks for any breakage of elastic fibers or stitches and for any loss of function after stretching.
Like the fatigue test, you can also test elasticity in a lab using a tensile testing machine to determine the exact properties of the elastic. While an on-site test checks more limited function, many garment importers still find the test helpful to assess the durability of elastic components.
Specify a general inspection level sample size in your QC checklist for stretch tests
The stretch test isn’t very time consuming and the quality of elastic can vary from piece to piece. That’s why garment quality professionals often suggest conducting this test on the full general inspection sample size, rather than on a special inspection level sample or fixed number of pieces. The sample size “G” in the table below refers to whatever general inspection level you’ve chosen for visual inspection—whether GI, GII or GIII.
The stretch test can also apply to other parts of a garment aside from accessories. For example, inspectors often perform this test on elastic fabric, an essential component of many lingerie, swimwear and sportswear garments.
4. Check buttonholes for stitching defects
Buttons are one of the accessories of a garment most susceptible to falling off. Many manufacturers even sew an extra button to the garment or include one in the packaging for consumers as a replacement.
But that doesn’t mean you shouldn’t pay attention to button defects during inspection. In fact, since buttons are so susceptible to functional and durability issues, evaluating buttons and buttonhole stitching should be an even higher priority during clothing inspection.
Fatigue tests and pull tests can help you verify the function and durability of the button itself. But a button without a functional buttonhole doesn’t serve much purpose. There are no particular on-site tests for the buttonhole itself. But your inspector should look out for a number of quality defects related to buttonhole stitching during garment inspection.
How to classify buttonhole defects for garment inspection
Most quality issues related to buttons are classified as “major” defects using AQL standards. But you may choose to class them differently based on your own quality expectations. Major defects are quality issues that lower the value or usability of a product and might cause a customer to return it (related: How to Classify Defects for Garment Inspection).
Defects related to buttons can hurt sales and brand perception. So most garment importers generally prefer to limit these as much as possible. Some common examples of buttonhole defects and the problems they cause are:
- Incomplete, skipped stitches or untrimmed threads around the buttonhole can cause the button to catch or make it difficult to fasten the garment.
- An improperly sized buttonhole can make the garment easily come unfastened or difficult to fasten at all.
- Buttonholes sewn vertically when they should be sewn horizontally and vice versa can affect function and style of a garment.
List these and any other buttonhole defects along with their defect class for reporting purposes directly in your QC checklist.
As with other garment defects, inspectors will usually check all pieces in the main, general inspection level sample for these defects as part of visual inspection.
Applying a specific tolerance for the acceptable number of major defects in a sample using AQL or a similar standard can make your inspection results clearer and more actionable (related: The Importer’s Guide to Managing Product Quality with AQL [eBook]). Include both your sampling plan and any AQL or other tolerance for each defect class in your checklist.
5. Visually check for accessory nonconformances during clothing inspection
The most important checkpoint for accessories is to check that they conform to your specifications, as provided to your suppliers.
Imagine choosing a neutral, inconspicuous black button for a professional suit jacket, only to receive a jacket with a lime green button on it! While this is an extreme example, there are many ways accessories might vary from your specifications. Specifications for accessories could include color, style, brand, size, placement and any other physical attributes.
For example, some designers and apparel manufacturers prefer to use particular branded accessories. YKK-branded zippers are particularly popular among garment importers. But SBS-branded zippers, from a Chinese brand, might be more readily available to your supplier in China. Without a pre-shipment inspection to verify, you could unknowingly buy garments with the wrong zipper installed.
How to classify nonconformances in your QC checklist
Like garment defects related to buttons, many nonconformances and visual defects are also classified as major defects during garment inspection.
Depending on the severity of the issue and its prevalence in the inspection sample, some importers may instead choose to classify these issues as minor defects. While these standard garment defect classifications are a helpful starting point, you should always consider your own customers’ tolerance for quality issues when drafting clothing inspection criteria.
Conclusion
Accessories can transform a basic assortment of cuts of fabric into a fully functional and stylish piece of apparel. Most of the above garment defects related to accessories can easily be repaired or reworked before the goods have left the factory. And there’s usually little danger of introducing new defects into the garment when reworking these issues. If a button is missing, the factory can simply sew one on right away.
Of course, accessories are just one part of a garment. And accessory checks should only be one part of an overall complete garment inspection. Don’t forget to conduct other important clothing inspection checkpoints, such as checking measurements, sewing stitches, fabric quality, packaging and clothing labeling.
If you’ve got a good handle on all these, you can be confident that quality problems won’t get in the way of your success as a garment importer.
Do you include any other on-site tests or checks in your garment inspection criteria? Share your tips or questions in the comment section below!
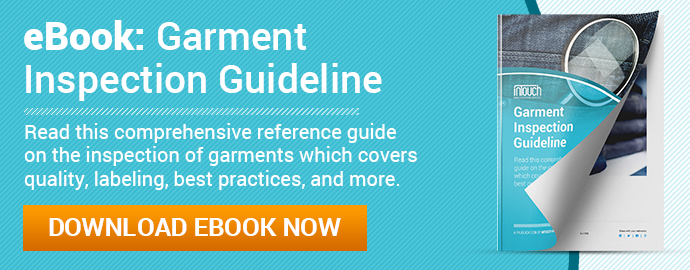