“The factory representative did not allow the inspector to perform the carton drop test”.
Imagine reading this remark in the report the morning after your products were inspected. A number of questions might run through your mind right away: Is the product packaging durable? Will my product be damaged during shipment? Is my customer going to return the product or request a refund?
Packaging quality control is often overlooked by both importers and factories, as both parties often spend far more time considering requirements for the product than for the packaging. But if you neglect packaging inspection or omit a crucial packaging check, your product might not make it across international waters and into your customers’ hands in new condition (related: Packaging Inspection Guideline [eBook]).
Checking for proper packaging materials and methods is an essential step of pre-shipment inspection. But you can’t just schedule an inspection at the factory without a little preparation first. The best defense against packaging issues is providing packaging requirements to your supplier and inspection staff well before inspection.
So before you shoot off that email to your supplier with your packaging requirements, let’s take a look at some of the best ways to prepare for packaging QC.
Why do you need to address packaging requirements before inspection?
The product packaging phase usually follows production. And inspection can occur at various times before, during and after production. But in general, only pre-shipment inspection, which is conducted when at least 80 percent of the goods are finished and packed, includes packaging checks.
Factory workers don’t normally pack units one by one as they come off the production line. Instead, they typically wait until production is close to finished before packing goods in bulk. Since it’s difficult to check packaging until so close to shipping, shipping delays often result when you find serious packaging issues during inspection.
And as we’ll see next, many suppliers outsource packaging production to sub-suppliers, which can stretch delays further if factories need a sub-supplier to send replacement packaging materials. You can avoid these last-minute delays by addressing packaging requirements early and limiting your risk of encountering problems during inspection.
How to address packaging with your supplier before inspection
Have you ever played the children’s game “telephone”, or "Chinese whispers”? The first person in a group whispers a message into the ear of the person next to them, and so on, until the last player announces aloud the message they received. The relayed message is almost never exactly the same as it started out.
The “Chinese whispers” of the importing business is communicating your product requirements to your supplier and hoping the product comes out as you intended. If it was just a matter of communicating with a single factory contact, it might be an easier game. But more often than not, factories abroad will contract some parts of production, including packaging, to various sub-suppliers.
Most importers don’t know all the sub-suppliers within their supply chain, much less how to contact them about their packaging requirements. So the best way to ensure that your packaging meets your standards is to provide clear packaging requirements to your supplier far in advance of production and inspection.
1. Set expectations in your PO to avoid resistance to packaging tests
While independent inspection is pretty common in the manufacturing industry these days, some suppliers might still resist parts of an inspection they think are unnecessary or difficult to pass. For example, factory staff might forbid inspectors to perform certain packaging checks that can damage the goods inside, including the carton drop test (related: 5 Packaging Quality Control Checks No Importer Can Afford to Skip).
The best way to limit supplier resistance to packaging checks is to finalize and confirm packaging requirements with the supplier in your PO before placing the order. This ensures that on the day of inspection factory staff can't claim they were unaware of or misunderstood your requirements. You’ll want to include information regarding:
- Who will conduct inspection: such as yourself, a full-time inspector or a third-party inspector
- When inspection will occur: e.g. you might choose to conduct inspection during production, as well as checking packaging during pre-shipment inspection
- What packaging tests you require before shipping: these often include simple checks for inspectors to perform or more sophisticated tests requiring an accredited lab
Remember that third-party inspectors cannot force suppliers to allow a particular test to be conducted. As they’re independent of both the factory and you, the customer, third-party QC providers need factory workers’ full cooperation in order to carry out inspection.
If you’ve made these expectations clear in the PO upfront and your supplier is still uncooperative, this might be a sign that you need to find a new supplier that respects your requirements.
2. Provide packaging quality control requirements in a QC checklist
Aside from setting expectations for checking your product’s packaging before shipping, effectively communicating your packaging requirements to your supplier will help you prevent problems. Many importers rely on a QC checklist to clarify various packaging requirements. A QC checklist is essentially a sorted, itemized list of your product and packaging requirements, some of which typically include:
- Packaging materials: e.g. retail & master cartons, polybags, packing peanuts, etc.
- Packing assortment: e.g. units per retail carton, retail cartons per master carton
- Sealing method: e.g. staples, clear/opaque tape, plastic/metal straps, glue
- Carton labeling: e.g. handwritten/printed labels, carton markings, barcodes
Your QC checklist should be detailed enough that it doesn’t leave questions unanswered but concise enough that production and inspection staff can quickly find the information they need. The length of a checklist usually varies depending on the complexity of the product and packaging.
Many importers list UPCs, barcode numbers and shipping marks on a separate sheet to ensure this information doesn’t get lost within the QC checklist. You might also consider sending a detailed list of instructions with photos for visual reference on how to properly package your product.
You might want to translate your QC checklist so that your requirements are listed in both English and your supplier’s native language. While the supplier contact you communicate with regularly may speak English fairly well, production and QC staff at the factory likely won’t. Providing your requirements in their native language can greatly reduce your risk of quality problems due to misunderstandings.
If you’re unsure what points to include in your checklist, third-party QC providers can often help. They can use their experience with similar products and packaging to advise which tests or inspection criteria may be relevant.
List on-site tests for packaging inspection in your QC checklist
Another important point to include in your QC checklist is any testing you require during inspection, along with your tolerances for issues or deviations from specifications (related: How To Address On-Site Product Testing In A QC Checklist). On-site testing for packaging can range from the more general, like a barcode scan check, to more packaging-specific, like a blister pack impact test, hang tag fatigue test or retail box gluing check.
The below table shows how to organize information regarding packaging quality control checks in a QC checklist. Note that each check point includes information on both their desired inspection level and their tolerance for quality issues.
When it comes to some packaging tests, you often won’t need to inspect a large sample size. This checklist excerpt shows an “S-1” inspection level, which refers to a special inspection level under the AQL sampling system. S-1 is the smallest of special inspection levels and is used here because these packaging tests tend to yield similar results across all units. The factory isn’t likely to switch printing files mid-production or start using a differently sized box for half of the units.
Some issues are less critical and you can allow for some nonconformance. For example, you might consider allowing for slight variation in printing colors for retail packaging artwork and could provide a list of several acceptable Pantone colors. Other packaging mistakes are critical and will need to be reworked before shipment. For instance, the wrong UPC code would result in a barcode that neither your warehouse staff nor retailer could scan for inventory or purchase.
Confusion over who will provide what equipment often leads to an inability to conduct certain tests. You can prevent this by including in your checklist any tools or equipment required and which party will provide it. Fortunately, most standard packaging tests don’t require expensive or cumbersome equipment. Your supplier’s factory should have an industrial scale on-site to weigh packaging. And your inspectors should be able to bring basic tools, like a measuring tape and a barcode scanner, with them to the factory.
3. Send all necessary retail branding and artwork files to your supplier and inspectors in advance
Imagine if your supplier misspelled your product name or printed your logo in the wrong color on your retail packaging. What would your customers think if they looked at your packaging and saw these kinds of issues before even seeing the product itself?
When it comes to packaging QC, incorrect spelling, wording or graphics on retail packaging are among the most common packaging defects found during inspection. And these often stem from not getting the necessary artwork files and retail branding in the hands of the right supplier staff ahead of production.
You should always send the design files for any printed materials to your supplier in advance of production. You might require printing for a number of items, including hang tags, cartons, polybags, instruction manuals, paper inserts or brochures. With the native design files, suppliers can then send your requirements to their sub-suppliers with no danger of mistranslation.
Similarly, inspection staff can overlook any branding or artwork problems if you haven’t provided them with the specifications before inspection. Inspectors often print off your requirements or view them from a tablet or laptop at the factory to match your requirements with the product and packaging features found during inspection.
Request a product sample with retail packaging from your supplier
Sending design files to your supplier before production can certainly help prevent issues with retail packaging. But you can go a step further to ensuring your retail packaging conforms to your requirements by also requesting a product sample with its retail packaging before production.
By requesting a sample early enough before production, you can often confirm many facets of your product packaging on your own, with little equipment or time required. Some essential branding and artwork features to check on retail packaging can include:
- Colors used in retail graphics and text, often measured using a standardized system like Pantone
- UPC codes, barcodes and other carton labeling
- Brand logo, text and graphics on cartons
- The content of any printed brochures or instruction manuals included with the product
The peace of mind you get by confirming your supplier’s understanding of packaging requirements will be well worth the time you might spend requesting, checking and approving a sample.
Conclusion
Hopefully you now feel prepared to send off that email to your supplier and set your expectations for packaging inspection. The process for preparing for packaging inspection can be split into three clear steps:
- Set packaging inspection requirements in your purchase order when placing your order
- Provide both supplier and inspection staff with a QC checklist before production, complete with clear packaging requirements
- Provide all retail packaging design files to supplier and inspection staff, and if possible, request a product sample with retail packaging before production
Providing clear requirements to your supplier not only helps you get the packaging you want. The same principles described here have also helped countless importers get the products they want. Regardless of whether your concern is your product or your packaging, in the world of manufacturing an ounce of prevention really is worth a pound of cure.
Still need more help preparing for packaging inspection? Download our comprehensive guide to packaging inspection below!
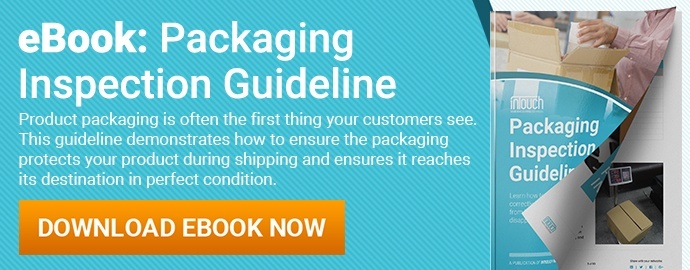