Let me guess. You’ve probably never given much thought to how to effectively destroy your own products. After all, why would you want to destroy something you’ve invested thousands of dollars and countless hours developing?
But what are you supposed to do with defective products you don’t want to sell, or can’t sell, to your customers? When you’ve exhausted all other options, including product rework, should you just tell your supplier, “I don’t want these products,” and let them deal with them?
Blindly trusting your supplier to dispose of your rejected goods usually isn’t a good idea. You’d be risking customer complaints, loss of intellectual property (IP) and even legal liability if your supplier chooses to sell your rejected products behind your back on the grey market.
You might be tempted to just stomp up and down on your defective products to release some frustration. But there are a number of more effective destruction methods available to you (related: Total Product Destruction: The Importer’s Guide [eBook]). So let’s take a look at how to decide on a total product destruction method that’s best for you and how you can verify it’s effective.
Which destruction method will ensure your supplier can’t sell your rejected products?
Before deciding on a product destruction method, pre-shipment inspection is a common first step to understand the type, severity and frequency of quality issues in your products. Product destruction may be an unnecessary and wasteful method of handling defective products if there are other effective defect management solutions available that will leave your goods intact.
If it’s clear the defects or quality issues found in your products have rendered them unsellable beyond remedy, destroying the affected goods is often the best way forward.
The most important factor in choosing a product destruction method should be whether the method ensures your product can no longer be sold or used. Common destruction methods include:
- Shredding of softline goods and materials like garments, footwear, textiles and paper using an industrial shredder or manual labor
- Crushing of hardline goods with a steamroller or other industrial equipment
- Incineration of combustible materials and products, particularly if the product poses a danger if not completely destroyed
- Recycling of safely reusable materials like paper, packaging materials, glass, plastic or electronic components
While simply disposing of products in the trash might seem easier or cheaper than the above methods, there are a few risks associated with failing to effectively destroy your product.
Why you need to ensure your defective products can’t be resold
What’s the big deal if a defective product isn’t destroyed? You could face serious consequences if you can’t adequately control rejected inventory. Defective products can:
- Pose a danger to consumers, for which you or your business could be held legally liable
- Damage your brand’s reputation if consumers unknowingly buy your branded, defective goods through unauthorized channels
- Put your IP at risk if factories sell your defective products to competitors or otherwise give rise to copycat products
Who would ever want to sell the inventory you’ve rejected? Well, your supplier might. You may have indicated you aren’t willing to pay for these substandard goods. But who’s to say there isn’t another buyer out there that is?
Factories can often sell defective products at a lower price in grey markets. They might also be able to sell them to a competitor of yours, particularly if your rejected product is a new product or prototype not yet available to the public. For consumers shopping on ecommerce channels like eBay and Amazon, they might not be aware you rejected these goods. Instead, they just recognize your branding on the product and assume it comes from a legitimate source.
When quality issues arise, many consumers will probably revert back to your company for a solution to their complaints. If you’re lucky, you might be able to just refund or replace the product. But in worse cases, a safety issue with the product could lead to consumer injury, or even death. Whether from negative online reviews or a lawsuit, your brand’s reputation is likely to suffer if substandard goods leak through unapproved distribution channels.
Certified destruction and disposal protects consumers from unsafe products and protects your brand’s reputation by keeping your rejected goods off the market. The destruction method that best ensures your product can’t be sold will be the most effective option.
Which product destruction method is most cost-effective for you and your supplier?
Cost-effectiveness is another factor both you and your supplier may consider important in choosing an appropriate destruction method for your rejected goods. There might be several methods for sufficiently destroying your product, but some might cost more than others. Multiple factors can contribute to the cost of total product destruction services, including:
- Equipment available on-site at your supplier’s facility
- Manpower required and labor costs for destruction personnel
- Cost for transportation of defective products to destruction site and product disposal site
Total product destruction services are often billed, in part, based on the labor time required to complete the service. So you’ll need to account for this along with all of the above factors when deciding which method is most cost-effective.
For instance, shredding a softlines product manually with scissors will likely take more time than using an industrial shredder. But most factories won’t have an industrial shredder on-site. If you have to pay to rent an industrial shredder and transport the goods to a destruction site, using a shredder could end up costing more money than simply shredding the product with scissors.
Who should pay for total product destruction services?
Whether you or your factory should be responsible for covering the cost of destruction will usually depend on the terms you agreed to before production.
A manufacturing contract drafted by a local lawyer and in accordance with local laws in the manufacturing country can help clarify responsibilities and protect your interests. But at the very least, you should have an informal discussion, before placing your order, about who should pay for costs related to defective products, including:
- Rework for any product defects that can be resolved through repair
- Re-inspection to verify rework or repairs
- Product destruction services for rejected products you cannot sell
- Chargebacks or replacement goods to refund rejected products
Many importers make the mistake of waiting until they receive a shipment to address rejected products with destruction. And this method can offer more direct oversight and assurance of destruction’s effectiveness.
But it’s almost always less expensive to proceed with destruction in the same country where the products were manufactured. It generally doesn’t make much sense to pay for overseas shipping just to destroy substandard goods that you can’t sell. And once the goods have shipped, you have little room to negotiate sharing the cost of destruction services with your supplier.
The last cost you’ll need to consider is whether to hire a trusted third-party agent to oversee and verify the destruction process in the manufacturing country.
How to verify total product destruction remotely
Choosing the right destruction method is important. But choosing who destroys your products is also vital. If your supplier has agreed to pay for destruction but doesn’t provide any proof that destruction actually occurred, chances are it probably didn’t. Instead, they probably chose to sell the goods elsewhere to recoup their losses on your order.
The moment you reject a quantity of goods, your supplier has already lost money on the order. They’ve already bought all the necessary raw materials, components and packaging for the defective products. And depending on your agreement with them, they might have to cover the costs of replacing these defective products. Given the choice between destroying the goods you don’t want and selling them to someone who does, many suppliers will often choose the latter.
This is a very real phenomenon among factories in developing countries. Without reliable oversight of the process, suppliers might not actually conduct destruction. To ensure your rejected products are actually destroyed, either one of your own staff, or someone independent from the factory, should be on-site to verify the destruction process.
If you can’t personally be on-site to oversee the destruction yourself, you can hire a trusted agent, such as a third-party inspector, to act on your behalf. Many third-party inspectors can give you clear documentation showing the destruction process to ensure your products were completely destroyed, just as if you were there yourself.
What information should your product destruction report include?
The agent overseeing your product’s destruction should issue you a report with details and photos of the process, similar to a report you might be familiar with for pre-shipment inspection. It may also be relevant to include a video recording of specific destruction processes. Your destruction report should verify every step of the destruction, with information and photos for each of the following processes:
- Pick up of defective products at factory location, including photos of all SKUs in their current condition before destruction.
- Loading and transport of defective products to destruction site, if applicable. Some factories won’t have necessary destruction equipment on-site.
- Destruction of defective products, including photos of destruction equipment and products after destruction is completed.
- Final product disposal, including transport to landfill and burial process, where relevant.
Your report should also specify the associated SKUs, PO number and quantities destroyed. And the agent should pay close attention to confirming the entire quantity of goods has been destroyed as intended. Otherwise, factory staff or workers from the destruction company might try to quietly set aside a number of units from the lot for resell or personal use.
Conclusion
Destruction is often seen as a last resort in defect management. And it can be hard to know if destroying defective products is wise in your particular situation. Destroying an order of goods to eliminate a problem you could have resolved through other means would be very wasteful.
But a professional third-party inspector can often provide some insight and advise whether destruction is necessary (related: 4 Ways Importers Conduct Product Inspection [eBook]). And while it might come at a cost, verified product destruction can be absolutely essential to protecting your brand and ensuring your rejected products don’t end up being sold through unauthorized channels.
Your chosen product destruction method will likely vary based on your product type and budget. Hiring a trusted third-party agent to oversee destruction will ensure it’s only your defective products that go up in flames, not your brand too!
Still not sure which destruction method is right for your product? Leave us a comment below and we’ll share our experience!
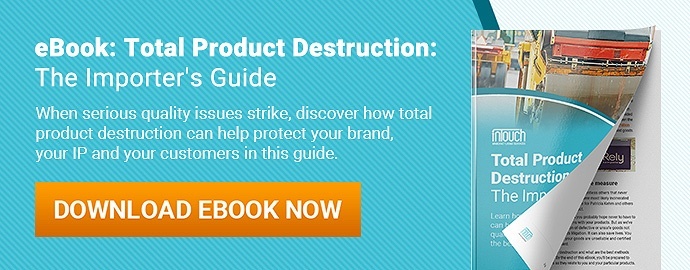