Did you know that an ISO-standard, 20-foot (6.06m) shipping container has a capacity of 33.1 cubic meters? That’s enough space to fit almost 100 household-sized washing machines!
It sure sounds like a lot of space. But have you ever actually taken a look inside a shipping container after it’s been packed with pallets and shipper cartons? Squeezing a maximum amount of inventory within this confined space without damaging the products can seem like tackling a jigsaw puzzle.
Loading your shipping cartons into the container is just one of the steps your products must go through before they reach your customer. Between choosing the right packaging materials, storing and handling the goods and passing through customs, there’s lots of room for delays or quality problems along the way. And packaging issues at any step in the process can lead to distributor refusal, customer returns and other problems that could mean “game over” for your business as an importer.
Luckily, these problems can be prevented with quality checks performed before shipping (related: Packaging Inspection Guideline [eBook]). Let’s explore the potential reasons why your product might not reach your customers in the right condition and how packaging inspection or testing can help you avoid them.
1. Packaging materials are crushed during shipping and handling
Like most importers of consumer products, you may choose to pack your products in cardboard shipping cartons before they leave the factory. Cardboard shipping cartons are light, inexpensive and can provide great protection from a number of outside elements. They’re also highly stackable for transport. But they’re not invincible. If your customers report that your inventory arrived in crushed shipping cartons, you might want to look into the following causes.
Stacking too many heavy cartons leads to crushing
As factories reach peak season and are juggling a high volume of orders at the same time, they might lack space for proper storage. So workers might store your cartons in different areas of the factory or even stack another importer’s product on top of yours. When using the proper packaging materials for your product, and when stacked appropriately, stacking shipping cartons for storage and shipment poses little harm to your product. But shipping cartons can easily get crushed during shipment if workers stack too many heavy cartons on the top of one another.
Improper packing assortment leaves your products vulnerable
Improper assortment of your products among cartons, such as packaging too many or two few units within a carton, can also weaken shipping cartons. For instance, an importer of decorative pillows might request factory staff to pack three pillows within one standard-sized carton. But if the factory instead uses a smaller carton to pack the same number of pillows, the top of the carton could expand and limit the number of cartons that can fit in a shipping container.
Over-packed pillows could also become deformed during storage and may not easily return to their original shape. If cartons are instead under filled, excess space can leave products free to move around during shipment and cause the cartons to collapse when stacked—both can damage the products.
Inadequate packaging materials don’t protect your product
Sometimes goods can arrive damaged because factory workers haven’t used suitable packaging materials for your product type. This could include using the wrong number of ply cardboard, cushioning materials or other packaging materials. This is especially important for heavy and bulky products that can dent, puncture or otherwise damage the cardboard carton. Double or triple-wall (5 or 7 ply) cardboard is often necessary for these products, rather than a single-wall cardboard carton.
What packaging quality control measures help prevent crushing during shipping and handling?
There are a few steps you can take to avoid over stacking, poor assortment and inadequate packaging materials. You may already be taking similar precautions with your products and can apply these without needing to invest any more time and other resources than what you’re already budgeting to quality control.
Clarify packaging materials and assortment in a QC checklist
Clarifying packaging requirements in a QC checklist is the easiest way to help prevent carton damage during shipment and verify your packaging materials and methods. An effective QC checklist typically has an entire section dedicated to packaging, as well as defect classifications for packaging defects. By collaborating with your suppliers on your checklist before production, you can be more confident that the finished goods and packaging will meet your requirements.
Combine a carton drop test and other packaging checks with product inspection
Pre-shipment inspection is one of the best ways to verify the requirements in your checklist. And a final inspection, which typically occurs after production is completed for more than 80 percent of goods, is considered the bare minimum amount of oversight for most importers. By this time, factory workers will likely have packaged some quantity of your goods. So your inspector will be able to examine packaging on site at the same time they check appearance, functionality and other aspects of the product itself.
A carton drop test is an easy packaging check for importers to include with inspection to verify the durability of packaging materials and simulate shipping conditions. The inspector conducts the carton drop test based on international standards and then checks the condition of both the carton and the products inside for any damage. If the product and packaging remain generally undamaged following testing, the carton will typically “pass” the test. But if there is significant damage, you may need to change your packaging materials or assortment method.
If you have a particular loading plan or procedure, container loading monitoring is another way to ensure your products have been packed and loaded properly.
Consider more rigorous packaging testing at an accredited laboratory
For most importers, clarifying packaging requirements in a QC checklist and conducting a packaging inspection with a carton drop test are sufficient to reveal any issues with carton stability. But more rigorous lab testing can provide an extra level of assurance for importers that need it. Both the edge crush test (ECT) and bursting strength test (BST) are relevant for testing the carton’s durability and stability, but they measure carton strength in different ways.
The edge crush test measures a carton’s compression strength by applying weight on the edge of a sample of cardboard standing on end. The bursting strength test instead applies weight to the flat side of a sample of cardboard to measure the box's ability to withstand external or internal forces. Any certified third-party laboratories should be able to carry out these tests according to international standards.
2. Poor packaging sealing or storage method leads to water damage or warping
If you’ve ever visited southern China, you’ve probably noticed the humidity. Between May and September, the sweltering heat and high humidity hit you in the face as soon you step off the plane. The same can be said of other major manufacturing locations in Southeast Asia. But what does humidity have to do with your packaging? A lot, actually (related: 3 Ways the Environment Affects Manufacturing).
Imagine you’re importing a notepad with a cardboard panel inserted within the leather cover. The notepads leave the factory in good condition. But you later discover the majority of the notebooks arrive at their destination with wrinkled covers—some with mold. It’s clear your packaging didn’t adequately protect your product during shipping. What happened?
Packaging materials can leave products vulnerable to water damage
If shipping cartons are improperly sealed, your products might suffer warping or water damage when exposed to temperature and humidity changes during transit. And cardboard can easily absorb too much moisture during shipment and shrink in size once the moisture evaporates. In this case, moisture likely penetrated your packaging and damaged the product, due to the way factory workers sealed and packed the cartons.
Factory workers commonly seal shipping cartons with tape. But you might need additional sealing or other materials, based on your product type. Products and materials that are especially vulnerable to warping or water damage include wooden products and furniture, electronics and paper and cardboard products like stationary and retail displays. You might consider packaging products in plastic sleeves or shrink wrap together with desiccant or silica packets to absorb any excess moisture.
The storage environment can damage products
You also need to consider how your factory’s environmental conditions might affect the storage of packaging materials. If left in a humid warehouse for too long, shipping cartons can fall apart during transit and leave your products vulnerable to damage. Cardboard shipping cartons can absorb moisture and mold if they aren’t stored appropriately. Even if a shipping carton looks outwardly usable, you’re putting your product quality at risk if you put your products in a carton that has been improperly stored in a humid warehouse.
Which QC steps help prevent product damage from humidity and temperature changes?
There are several steps you can take to limit the risk of your products being damaged by humidity and other climate conditions. These include auditing the supplier’s facility, clarifying expectations, inspecting product packaging before shipping and lab testing for climate conditioning.
Audit your supplier’s facility to verify proper storage methods
Many importers will perform an audit of their potential supplier’s facility before working with them for the first time. During a quality management systems (QMS) audit, typically based on the ISO9001 standard, auditors report on several areas of a factory that can affect the quality of the finished goods. Among those areas is the production and storage environment, where auditors look at conditions and verify the factory has a pest/mildew and humidity control system in place.
The results of an audit can help you catch potential problems with inventory storage and avoid working with suppliers that don’t use proper storage methods.
Clarify proper packaging and sealing methods in your QC checklist
As with packaging materials and assortment, specifying packaging sealing and storage method in your QC checklist helps ensure your supplier understands your requirements. The document will also come in handy later when inspectors can easily follow your specified packaging and sealing method and check them against what they find in the factory.
Check sealing and storage method during inspection
Whether you need your product sealed in plastic sleeves with silica packs or simply packed in polybags, pre-shipment inspection is the way to confirm your requirements. Inspectors commonly report the sealing method during most final inspections.
Often inspectors can also check the storage of your finished goods when they arrive at the factory. And random sampling, pulling cartons from various parts of the order, rather than from the same place, helps prevent workers from hiding any cartons with mildew, water or other damage. Your inspection report should include photos of carton storage so you can ensure the factory’s environmental conditions are sufficient.
Perform lab testing for climate conditioning
If you’re concerned about how your product and packaging will hold up during transit, you can address most climatic issues ahead of time by performing a lab test for climatic conditioning. During this test, a package or product is exposed to different controlled levels of temperature and humidity inside a calibrated test chamber. These tests usually need to be conducted in a third-party lab, because test chambers are quite expensive and factories typically won’t have them on-site.
3. Your product is seized or delayed at customs or your distributor’s warehouse
“Do you know how your goods are made, from raw materials to finished goods, by whom and where?”
This compelling question is posed by the U.S. Customs and Border Protection in their guide for commercial importers. If you don’t know the answer, chances are customs officials could seize your product. And your goods might not even make it to your customer at all, never mind in the right condition.
Knowing where and how your goods are made is not only important for customs compliance, but also for managing product quality and ensuring social compliance. Each product imported into the U.S. must be labeled with its country of origin. Otherwise, U.S. customs can seize your merchandise if it is “intentionally or repetitively marked in violation of country of origin marking requirements”.
Most importers don’t willfully circumvent customs laws in this manner. But even if you unintentionally provide unclear information on labels affixed to your shipping carton, you could still face processing delays at customs. There’s also a chance your goods pass through customs, only to have your distributor refuse them or charge you fees for mislabeling them (related: How Packaging Inspection Helps You Comply with Amazon FBA Standards).
What packaging quality control checks help prevent processing delays?
U.S. Customs and Border Protection provides a handy list of suggestions for faster clearance of your goods, including:
- Mark and number each package so customs staff can identify it with the corresponding marks and numbers appearing on your invoice.
- Show a detailed description on your invoice of each item of merchandise contained in each individual package.
- Mark your goods legibly and conspicuously with the country of origin unless they are specifically exempted from country-of-origin marking requirements.
- Package goods in a uniform manner so that each carton includes the same contents and values, and when possible, with only one kind of good in each carton.
Following the above recommendations will likely not only speed up customs processing, but should also make it easier for warehouse staff to sort and inventory your goods.
One of the most common issues with carton marking is that factory staff fail to number each carton out of the total number of cartons (i.e. “1 of 30”, “2 of 30”) by the time inspectors arrive on-site. Factory staff might be unsure how many cartons they’ll need to package an order until production is finished, especially with compactible goods like garments. So factory staff often handwrite these numbers on cartons after finishing all packaging. Asking your inspector to check for these markings can help hold factory staff accountable to filling out all of the necessary information before shipment.
A QC checklist is a great place to provide these instructions and all of the necessary information to include on your shipping cartons in one location. This can include purchaser’s name, PO number, item descriptions, carton dimensions, weight and country of origin. Both factory workers and your QC inspector can use this information to ensure all labeling and carton markings conform to legal and distributor requirements.
Conclusion
Broken products, warping, water damage and delays can all affect your relationship with your customer and your distributor. So when it comes to ensuring products reach their destination undamaged and on time, it’s always better to prevent and address these issues by clarifying requirements, auditing suppliers and inspecting and testing packaging prior to shipment.
Packaging may not be the first thing that comes to mind when you think of product quality. But it’s one of the most important factors determining whether your product reaches your customers in the right condition.
Do you have any horror stories of how your products were damaged during shipment due to packaging problems? Share your stories and solutions in the comment section below!
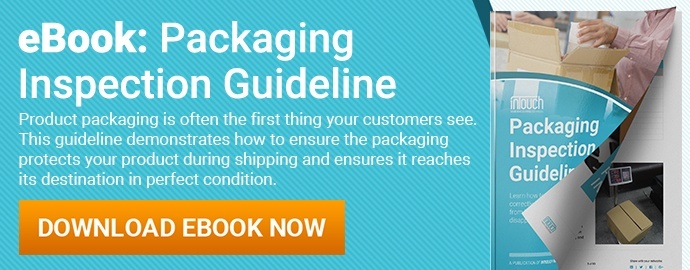