You never know what unexpected issues might arise as an importer sourcing abroad. When it comes to managing product quality and shipment deadlines, do you really want to be caught without a plan B?
Full-time inspection staff can be invaluable when you have a steady flow of QC needs year-round. With your own team, you can directly manage inspectors and book inspections based on your specific priorities.
But does hiring full-time inspectors mean you’ll never need third-party QC services? Not necessarily.
Depending on the number, training and location of your inspectors, your inspection team might not be able to meet all your inspection needs, all the time. Most importers with a local office hire only a few full-time employees, who sometimes also manage other tasks like sourcing and attending trade shows.
Though it may seem excessive, many importers use a third-party QC firm to supplement their full-time team on the ground (related: 4 Ways Importers Conduct Product Inspections [eBook]). Before you rely entirely on your full-time team, let’s look at how third-party inspectors may be able to help you out of an otherwise tight situation.
Increase production oversight when working with new products, suppliers or customers
Have you ever approved a product sample only to later find that the mass-produced goods don’t meet your standards? You might not always know your supplier’s limitations when placing an order. And it’s likely your supplier doesn’t fully understand your requirements, either.
You might be comfortable with just conducting one pre-shipment inspection for suppliers you’re used to working with and products you’ve manufactured before.
But in the beginning of a supplier-importer relationship, both parties are still familiarizing themselves with each other’s quality standards, working habits and communication skills.
With new suppliers, you won’t have previous inspection reports for reference to help shape expectations. The same uncertainty is common when distributing to new customers, as well. And for entirely new designs, you won’t have a history of quality issues at all.
That’s why importers often want added oversight throughout production when working with new suppliers, customers or products. Increased oversight through broader inspection can help you to:
- Set clear expectations early and demonstrate your commitment to quality to a new supplier
- Catch and address any product issues early before they affect the majority of an order by verifying production units match an approved sample or prototype
- Meet shipping deadlines by monitoring production status
How third-party QC can help you verify order status and quality throughout production
Your full-time inspectors might be able to provide increased support. But your team’s limited capacity could hinder their ability to adequately oversee production. Though clear communication can help you better manage inspections at multiple facilities, third-party inspection can help fill any shortage in qualified staff to ensure your suppliers are meeting quality standards and timelines.
For example, you may need an inspector on-site and to check production daily, or almost daily, a process sometimes called production monitoring. Can you spare a full-time employee for this time-consuming job? Maybe not.
You might also want to check 100 percent of an order before shipping a new product or when ordering from a factory for the first time. But if you only have one full-time inspector on-site, it might take your inspector multiple days to inspect the full order. You could send a third-party inspector to the facility as well, and together they could inspect the order in half the time.
How inspection companies can help you assess new suppliers
Auditing a supplier’s facility is a common and widely recommended step in vetting potential suppliers. Different types of factory audits can help you qualify a supplier before paying a deposit and committing to placing an order.
But auditing and inspecting require two different skill sets with auditors typically needing different training and certifications than product inspectors. Many third-party inspection companies employ both. And even if you have your own inspection team, a third-party auditor can help you evaluate new suppliers before production begins.
Close gaps in product knowledge among full-time inspectors
Many importers with full-time inspection staff face a knowledge gap that forces them to change their QC strategy. Like theirs, your full-time staff might only specialize in one specific product type and lack experience with inspecting others. This can make it difficult to expand your product range without compromising quality. Different products are typically evaluated using unique QC methods that can require specialized training. Most inspectors can follow a basic list of instructions. But it usually helps if an inspector has some background knowledge of industry standards for the product they’re checking.
Product-specific experience helps inspectors:
- Support you in developing inspection checklists based on relevant international standards and regulations
- Follow industry-standard procedures during inspection for on-site testing and defect classification for your product type
- Identify unexpected issues on site that might not be specifically addressed in your checklist
You may not have the time or resources to train your own full-time staff for a new product or hire a new specialized inspector. Hiring a third-party QC inspector with the relevant background can be a cost-effective way to fill that knowledge gap before it leads to unchecked quality problems.
Third-party inspection companies are often staffed with inspectors with a wider variety of product QC experience. These companies can provide tailored QC services for a range of product types with little preparation time needed (related: 5 Benefits of Inspection Companies with Diverse Product Expertise).
Third-party support for training full-time inspectors and factory staff
One often-overlooked service that third-party inspection companies can provide is specialized training. Wherever your team or the factory’s own staff may be lacking in product expertise, an inspection company with broader knowledge may be able to contribute.
For example, textile importers might hire third-party QC professionals to train their own or factory QC staff on the 4-point system for fabric inspection. Such a strategy can benefit you over time in a few ways:
- More consistent inspection and reporting methods and greater clarity
- Quality improvement as your supplier catches and addresses issues earlier in production
- Lower costs due to less dependence on outside inspections
Meet increased inspection demand during peak seasons
If you import outdoor sporting goods, luxury items or other products with seasonal sales trends, you likely know the feeling of needing to meet tight production and shipping deadlines during peak season. With promising sales on the horizon, there’s also added pressure to ensure goods meet customer expectations.
You may need to work with more manufacturers to meet the increased demand. But with a limited number of full-time inspectors, travel time and costs can add up quickly.
Factories aren’t usually conveniently located in the center of the biggest cities. Instead, they’re often on the outskirts of cities or in more remote areas. Especially in developing countries with poor transit infrastructure, inspectors might need to travel for a day or more between sites.
Longer travel times mean fewer and shorter potential working days for your inspectors. Waiting for your inspector to arrive on site for inspection could delay orders as you and your supplier wait for results before shipping. And the last thing you want ahead of a peak season is a backorder due to limited inventory.
Why third-party QC is more cost-effective during peak seasons
Your first response to a peak season rush might be to hire additional full-time auditors. But hiring more auditors to meet this demand won’t likely be cost-effective or time-efficient if you don’t also need those auditors in off-peak seasons.
Since full-time inspectors are usually salaried employees, you’d need to pay them even during downtime (related: Why You Should [or Shouldn’t] Hire a Full-Time Product Inspector).
Hiring third-party inspectors can be a cost-effective solution when you have QC needs at certain facilities on an infrequent or irregular basis. There’s no need to hire another full-time inspector to be based near a certain factory if you only occasionally need to inspect there.
When looking for a third-party QC firm to complement your existing inspectors, find one that can provide all-inclusive man-day rates to cut down on unpredictable travel costs.
Large third-party QC firms should have inspectors based in close proximity to most or all major manufacturing areas. This lets them more easily and quickly schedule inspections at multiple sites with only a few days’ notice.
A limited supply of full-time inspectors can only cover so much ground. Using third-party inspectors can help you be more efficient with your time and money, which can be a major stress reliever during peak seasons.
Limit your risk of corruption issues during inspections
Full-time QC staff typically spend a lot of time stationed at specific factories, working with the same factory staff over time. This can be beneficial in some cases to develop a closer business relationship and improve communication. But it also exposes you to greater corruption risk.
Inspectors carry an important responsibility to objectively measure and report on the quality and status of your products. This quickly becomes impossible the moment their judgement is compromised (related: Top 5 Issues That Can Affect QC Auditor Integrity).
Gifts and bribes from factory staff are obvious sources of corruption that can compromise inspector judgement. But integrity issues aren’t always so apparent.
Studies show that people evaluate their friends' behavior more positively than do strangers, regardless of their actual performance. If an inspector becomes too friendly with factory staff, they may become biased, favoring the factory’s priorities over yours.
What happens when your inspector becomes biased? They might:
- Overstate order status, leading to unpredictable production and shipping delays
- Inspect a smaller sample than agreed upon, underrepresenting results and providing less insight into the quality and status of an order
- Falsely report inspection results, including the kind and type of defects found, as well as on-site testing results
- Share your confidential information with factory staff or competitors
Rotate full-time inspectors with third-party QC
One of the best ways to reduce the risk of corruption issues is to rotate inspectors randomly between services. Rotating inspectors makes it harder for any one inspector to get too close with factory staff.
The downside of this approach is that it requires a larger fleet of inspectors. If you only have one inspector in Shenzhen and one in Beijing, for example, it doesn’t make much sense for these inspectors to travel over 1,300 miles at a time between services.
If you have a small full-time team, supplementing it with third-party inspectors might be the answer to your integrity concerns. Scheduling periodic third-party inspections will keep your supplier on their toes and prevent full-time inspectors from getting too close with factory staff.
Rotating inspectors also gives you the added benefit of spotting any integrity issues revealed through discrepancies in reporting.
For example, does your supplier usually pass inspection when a particular inspector is assigned but fails a subsequent inspection following the same methods with a different inspector? This might indicate the first inspector’s integrity has been compromised.
How to identify an inspection firm with sound integrity policies
A third-party inspection firm is only effective when they can be trusted to report honestly and accurately. When hiring a third-party inspection firm, be sure to look for some key indicators of strong integrity policies:
- A complete Code of Ethics or similar documentation that specifically addresses integrity concerns
- A large enough pool of available inspectors to allow for regularly rotating inspectors
- Routine and random internal auditing of inspectors to assess their performance in the field
- Hiring practices that weed out inspection candidates without a mature understanding of integrity risks and how to spot unethical behavior
These safeguards will ensure that your third-party inspectors dependably protect your interests, rather than falling susceptible to corruption.
Conclusion
With full-time QC staff, you may think hiring a third-party inspector is overkill. But there are times when supplementing your team with third-party inspectors can add value. And it’s always a good idea to have one on standby in case unexpected issues arise.
If there are any inspection services your own staff can’t cover, be sure to at least contact a third-party QC company for a quote. Most inspection companies don’t require long-term contracts, service minimums or other commitments—you’re free to start and stop services whenever you need.
If an inspection company has an inspector available nearby a supplier’s location, hiring them might even save you money over relying on full-time staff.
Do you use a combination of full-time inspection staff and third-party inspection services to meet your QC needs? Share your experiences in the comment section below!
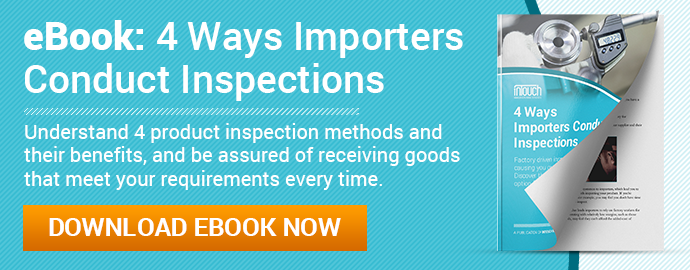